Aqui gostamos de automóveis! E como “amantes” de automóveis, o que é produzido cá também merece um cantinho especial. Não apenas por ser feito cá, representando vários milhares de postos de trabalho, mas também, e acima de tudo, pela forma e empenho com que é feito e que, em alguns casos, já tem merecido reconhecimento além fronteiras. Foi por isso que fomos conhecer cada um dos produtos nacionais que estão atualmente em produção. Aproveitando o feriado nacional do 10 de junho, dia de Portugal, aqui está a “nossa seleção” que representa a nossa produção automóvel nacional. Um especial que muito orgulho nos deu escrever. É caso para dizer que “o que é nacional, é bom!”.
Já lá vai o tempo dos Alba, dos Edfor, do Portaro, do Sado ou do UMM. A verdade é que se recuarmos muitos e muitos anos, a lista de modelos automóveis que compõem a produção nacional é até bastante diversificada. Mais recentemente conhecemos as monovolumes Sharan, Alhambra e Galaxy, ou ainda modelos como o VW EOS ou o VW Scirocco. As primeiras responsáveis pelo legado polémico que ainda hoje assombra o mercado automóvel. A famosa exceção na lei para considerar os monovolumes produzidos em Palmela como Classe 1 nas portagens nacionais. Adiante… anos depois, Portugal ainda tem produção automóvel, mas são poucos os modelos conhecidos do público em geral.
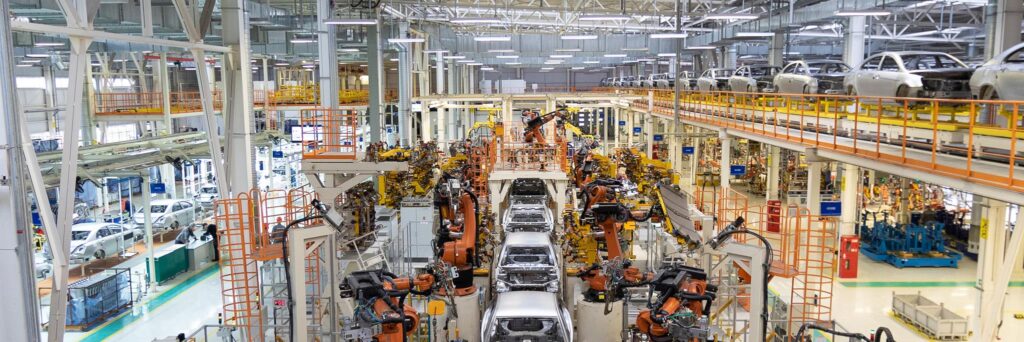
Comecemos por enquadrar as partes num todo. Vamos simplificar o processo para que não se torne um artigo demasiado maçador.
Um Puzzle gigante…
Construir um automóvel é, passe a expressão, como montar um Puzzle gigante, com milhares e milhares de peças. Contudo, tudo começa com muitas folhas de metal, tipicamente dispostas em grandes rolos. Estas são fundidas, forjadas ou estampadas em prensas e dão origem aos milhares de componentes que formam as carroçarias e os chassis dos automóveis.
Nas fábricas, as áreas dedicadas à carroçaria fazem a junção dessas peças, normalmente executada por robôs de soldadura. Dessa forma já é visível aquilo que vai ser a estrutura do automóvel, com portas, capot e mala. Em seguida, é com uma carroçaria completa que o veículo segue para a zona da pintura, onde recebe o tratamento anti corrosão e a tinta que lhe atribui a cor.
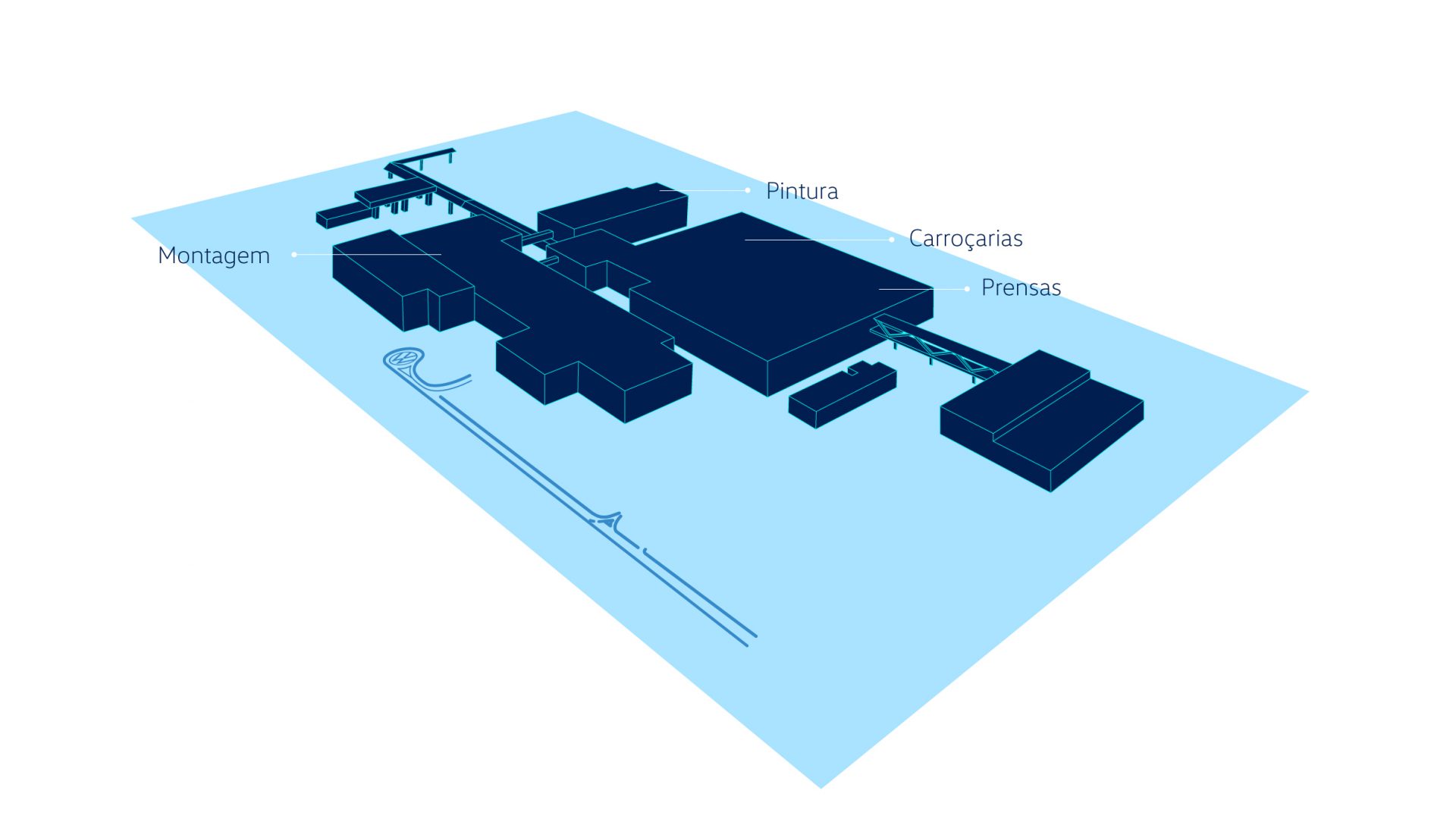
Posteriormente inicia-se a montagem final do Puzzle. Nesse momento as carroçarias recebem todos os componentes. Assim, a parte elétrica, o motor, as suspensões, as rodas, o interior e os vidros são apenas alguns dos milhares de peças que chegam ao seu destino final. É durante este processo que é feita a associação do nº de chassis com o nº de motor, como que o “bilhete de identidade” que acompanhará aquele chassis até ao final de vida do veículo. Logo após a montagem são feitas as verificações de qualidade e temos mais um automóvel a rolar na estrada!
… montado peça por peça!
Outro dos processos utilizados na construção de veículos são os CKD (Completely Knocked-Down). Estes são usados em três das quatro atuais fábricas portuguesas, PSA em Mangualde, Toyota Caetano em Ovar e Fuso no Tramagal. Desta forma, os milhares de componentes que constituem um veículo chegam ás fábricas completamente desmontados, daí o nome CKD, acrónimo de Completely Knocked-Down.
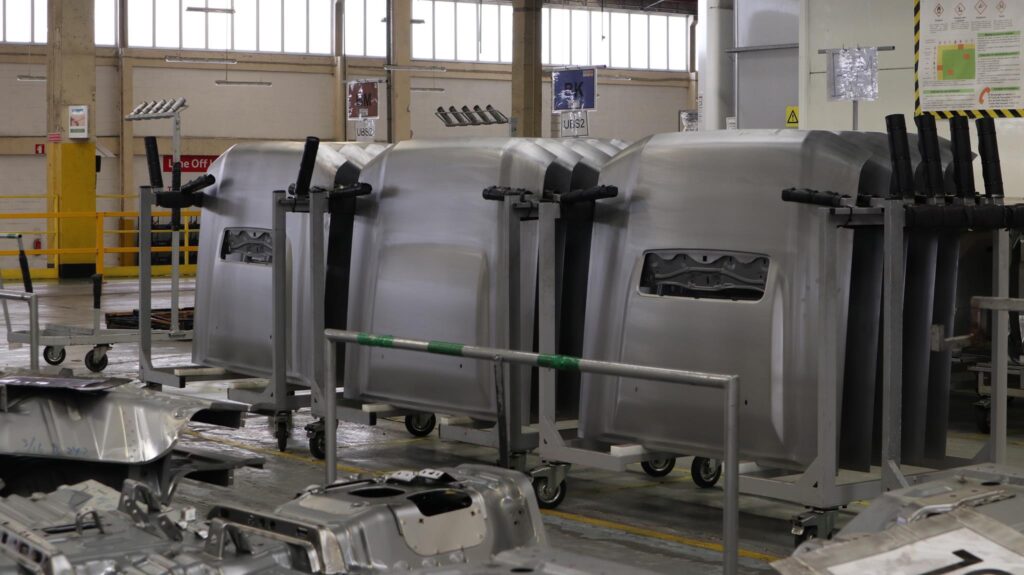
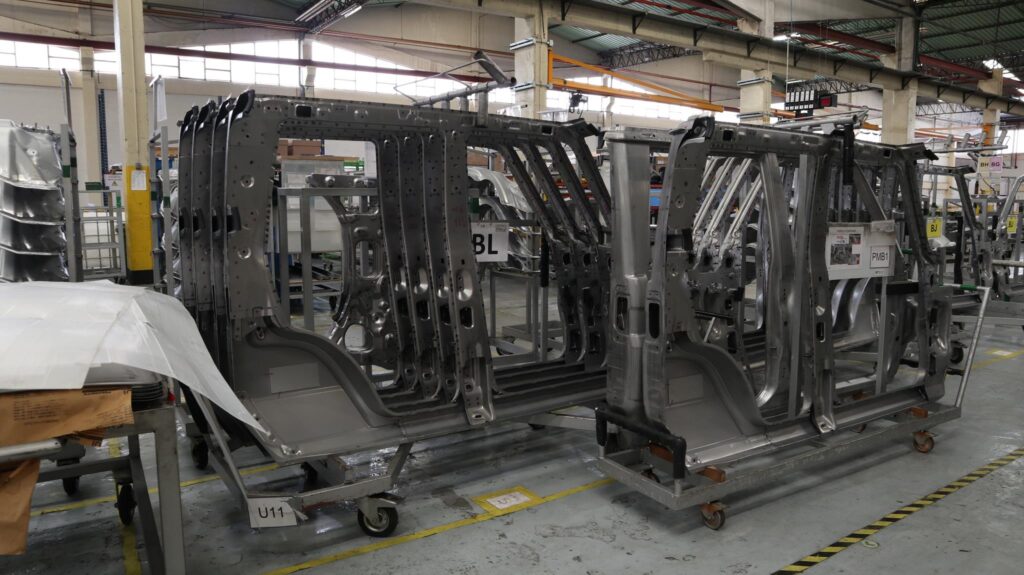
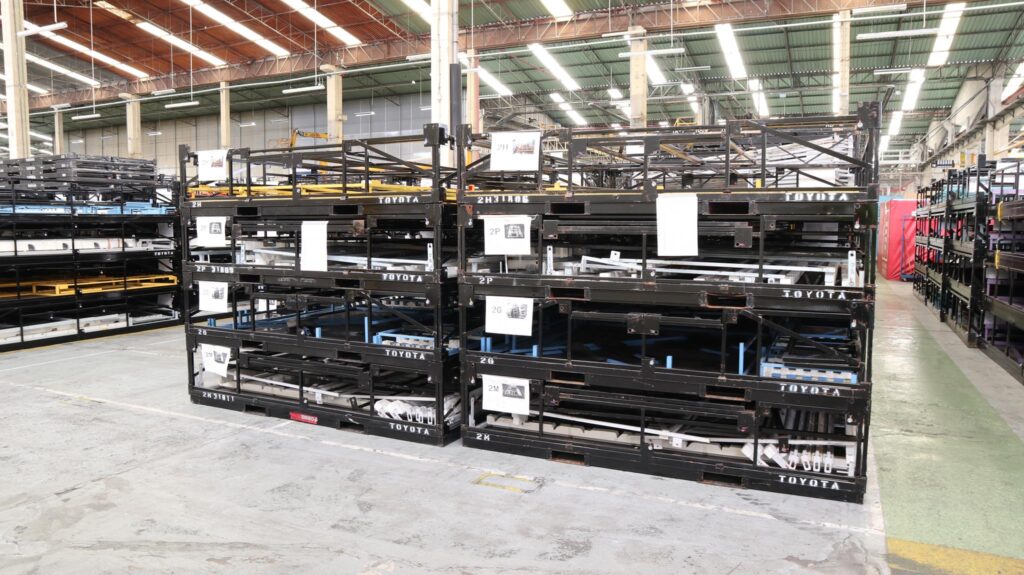
Neste método, todos os componentes vêm criteriosamente arrumados em contentores metálicos que são depois descarregados com o intuito de abastecer toda a linha de montagem. Nestes contentores vêm peças de carroçaria, chassis, interiores, motores e caixas, entre (muitos…) outros. São milhares de peças provenientes de outros países, e que chegam a cada uma das fábricas em Portugal para então serem montados chegando ao produto final em forma de Citroën Berlingo, Peugeot Partner ou Rifter, Opel Compo, Toyota Land Cruiser, ou ainda Fuso Canter. Atualmente, e por motivos de sustentabilidade e aproveitamento, os contentores vazios retornam à origem, em alguns casos completamente desmontados. Nós dissemos que era um Puzzle gigante...
Logística – Um enorme desafio
Conseguir que todos esses componentes cheguem ás fábricas a tempo de serem incorporadas na produção é um enorme desafio logístico e de cadeia de abastecimento. Desse modo, a partir de um dado volume de produção, torna-se essencial que os fornecedores de componentes estabeleçam pequenas bases operacionais junto ás fábricas, daí ser comum a menção ao termo “parque industrial”. Ademais, estas podem inclusive efetuar pré-montagens de componentes ou agrupar peças de vários fornecedores. Na prática, este é um processo complexo e que exige enorme coordenação entre as múltiplas equipas de cada uma das fábricas.
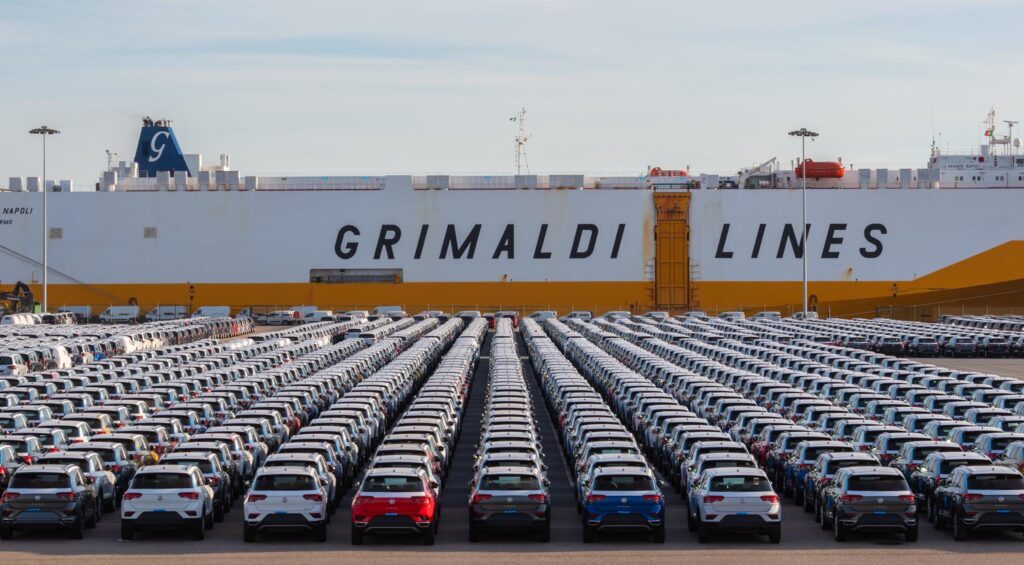
Do mesmo modo, é necessário assegurar o escoamento da produção acabada, habitualmente via camião ou comboio (Autoeuropa).
A componente económica
Com efeito, devido aos volumes de produção e a sua respetiva receita associada, a produção automóvel nacional tem um impacto económico muito importante, gerando mais de 2% do PIB (Produto Interno Bruto) nacional.
Em 2019 produziram-se 345 688 unidades, o nosso melhor ano de sempre, ao passo que em 2020 (um ano atípico por causa da pandemia) fabricaram-se 264 236 unidades, menos 23,6%.
Todavia, a relevância relativamente ás exportações é muito significativa, dada a pequena dimensão do nosso mercado. Assim, e de forma a caracterizar melhor o destino desta produção temos os seguintes indicadores.
Com efeito, dos veículos produzidos em Portugal em 2019, 97,3% foram exportados, 92,7% dos quais para o mercado europeu. Os países que mais recebem produção automóvel nacional são os seguintes:
- Alemanha (23,3%)
- França (15,5%)
- Itália (13,3%)
- Espanha (11,1%)
- Reino Unido (8,7%)
Em 2019, o volume de negócios da produção automóvel nacional atingiu um total de 4859 milhões de euros
- Autoeuropa: 3737 M€ (256,8 mil unidades)
- PSA Mangualde: 787 M€ (77,6 mil unidades)
- Mitsubishi Fuso Trucks Tramagal: 222 M€ (8795 unidades)
- Toyota Caetano Ovar: 52 M€ (2393 unidades)
- CaetanoBus Gaia: 98 M€ (16 unidades produzidas, 622 montadas)
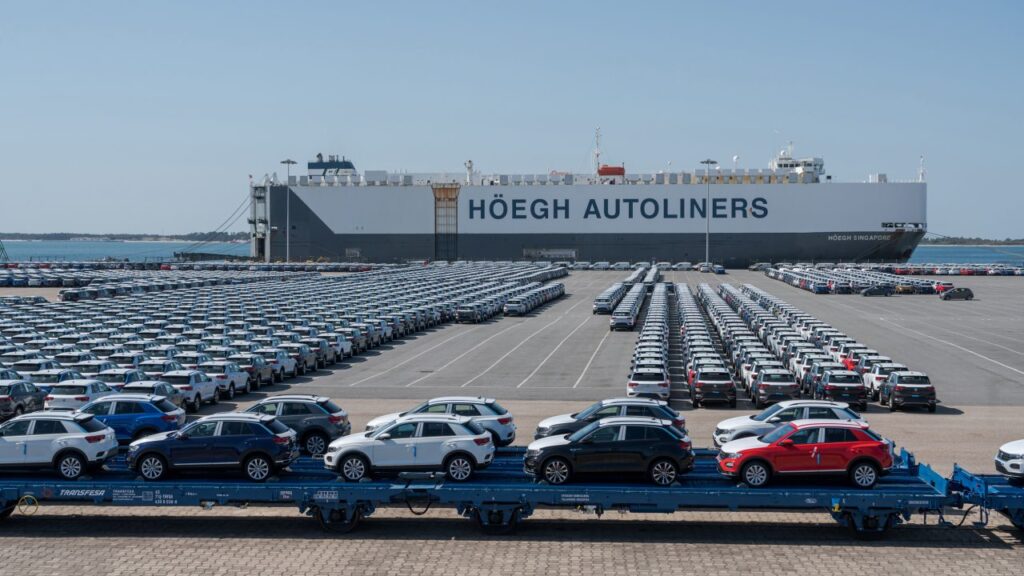
Neste artigo centramo-nos nos quatro primeiros, deixando de lado os autocarros montados pela CaetanoBus em Gaia, em virtude do seu reduzido volume. Similarmente, importa também realçar que além da capacidade fabril, a indústria portuguesa tem também uma longa tradição na área dos moldes e da fabricação de componentes.
Com um impacto muito importante no emprego nas zonas onde estão localizadas, as fábricas automóveis e as empresas de componentes que para elas trabalham são regularmente os maiores empregadores dessas regiões.
Assim, aquilo que procuramos fazer neste artigo especial é dar a conhecer a atual produção automóvel nacional, e a sua história. Nesse sentido, as atuais fábricas automóveis a produzir em Portugal são: Autoeuropa, Toyota Caetano, PSA e Mitsubishi Fuso.
1. Volkswagen Autoeuropa – Palmela
A Autoeuropa é, relativamente ás fábricas nacionais, a estrela da companhia. Localizada em Palmela, nasceu em 1991 num consórcio entre a Volkswagen e a Ford. Então destinava-se a produzir três monovolumes de sete lugares, a Volkswagen Sharan, a Ford Galaxy e a SEAT Alhambra, sendo que a laboração iniciou-se em abril de 1995.
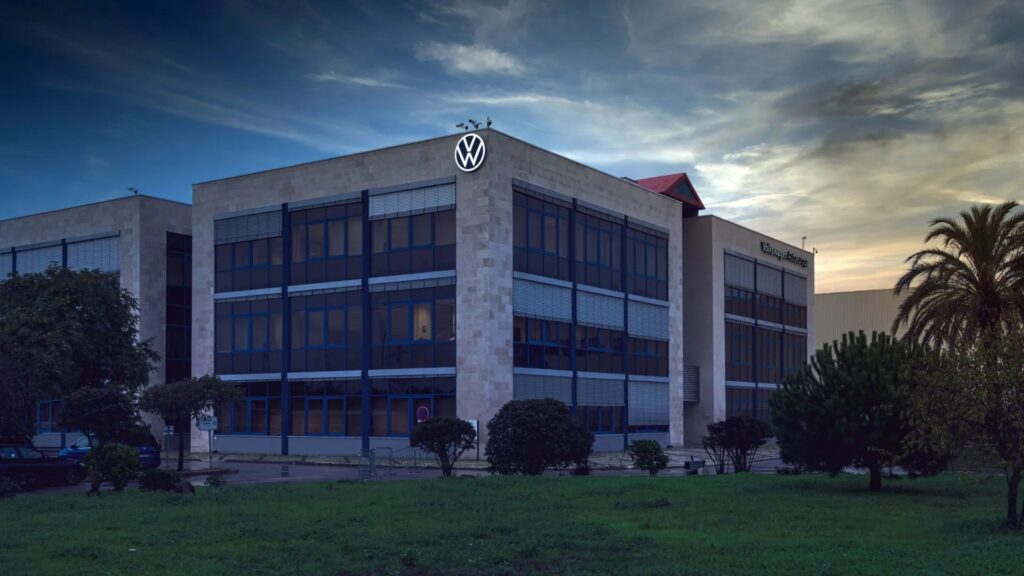
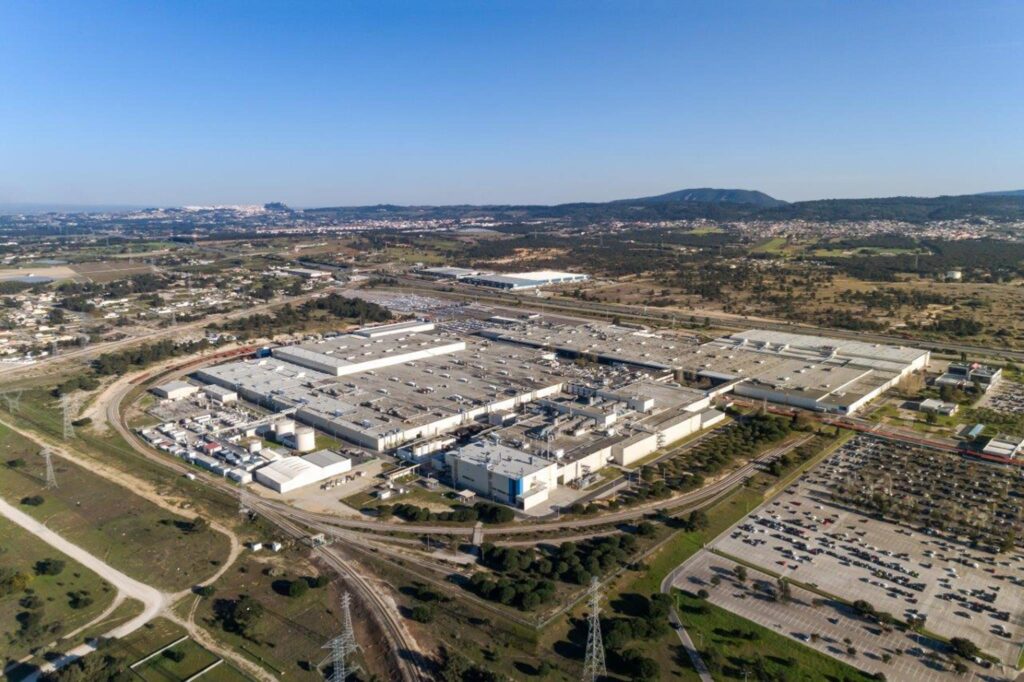
Em 1999 a Ford decidiu sair do consórcio e mover a produção da sua Galaxy para a Bélgica, tendo a Volkswagen assumido a totalidade da fábrica e mantido a produção. Assim, em 2006, esta recebe um novo modelo, o EOS, um coupé-cabriolet de capota rígida. Dois anos depois inicia-se a produção do Scirocco, um coupé derivado do Golf. Por outro lado a produção da Volkswagen Sharan e da SEAT Alhambra mantém-se, contudo com volume mais reduzido.
Mas é em 2017 que a fábrica vê um importante aumento da sua produção, com a entrada em cena do Volkswagen T-ROC, um SUV de segmento médio com elevado volume de vendas. Por conseguinte, o T-ROC permitiu-lhe atingir pela primeira vez a totalidade da capacidade de produção instalada, 890 veículos por dia e um total de 245 600 unidades no ano recorde de 2019.
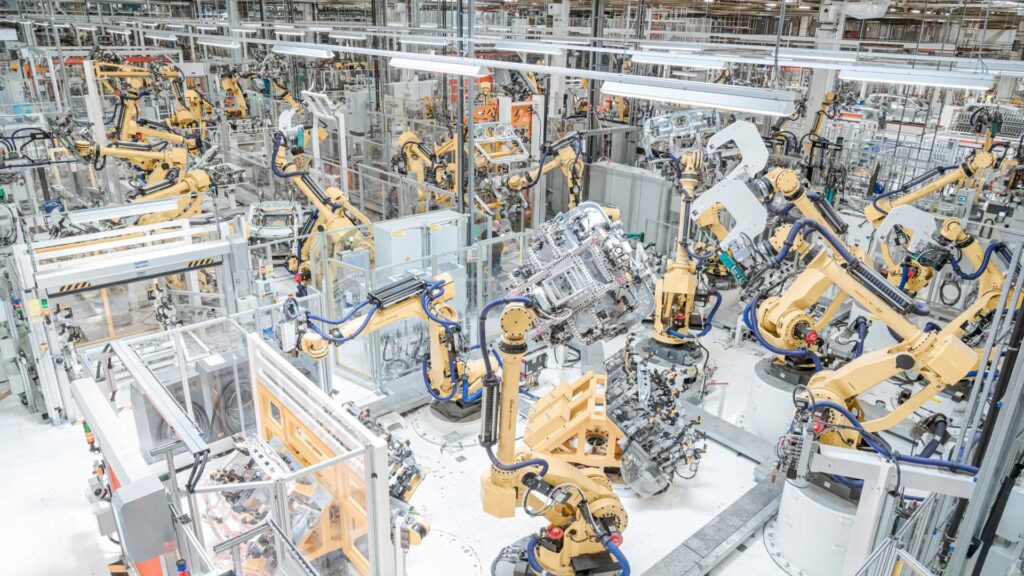
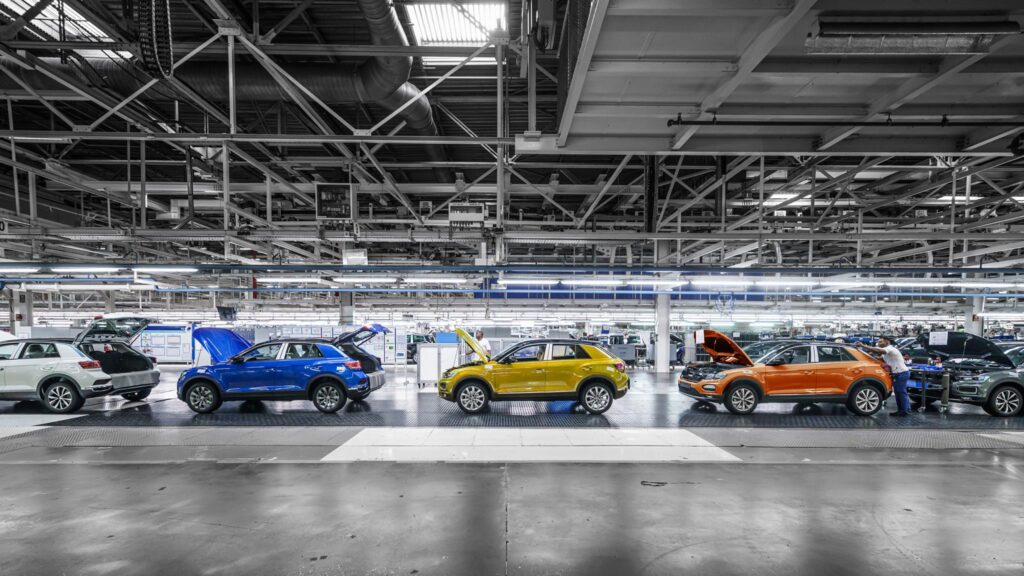
A Autoeuropa não produz apenas automóveis, mas também componentes para outros modelos e outras fábricas do grupo
Com toda a certeza a fábrica de maior dimensão em Portugal por larga margem, a Autoeuropa emprega diretamente mais de 5000 colaboradores e assume mais de 70% do total da produção automóvel nacional. Adicionalmente é também uma fábrica que inclui a totalidade do processo produtivo, ou seja, possui prensas e estampagem para efetuar muitos dos componentes das carroçarias. Não o faz apenas para si, mas também exporta 20 milhões de peças para 21 fábricas do grupo Volkswagen.
Os milhares de automóveis produzidos são maioritariamente enviados de comboio para o Porto de Setúbal. Daqui saem em navios para todo o mundo, mas especialmente para o continente europeu onde este modelo tem tido muito sucesso. Todos os Volkswagen T-Roc são produzidos na Autoeuropa em Palmela, assim como as VW Sharan e SEAT Alhambra.
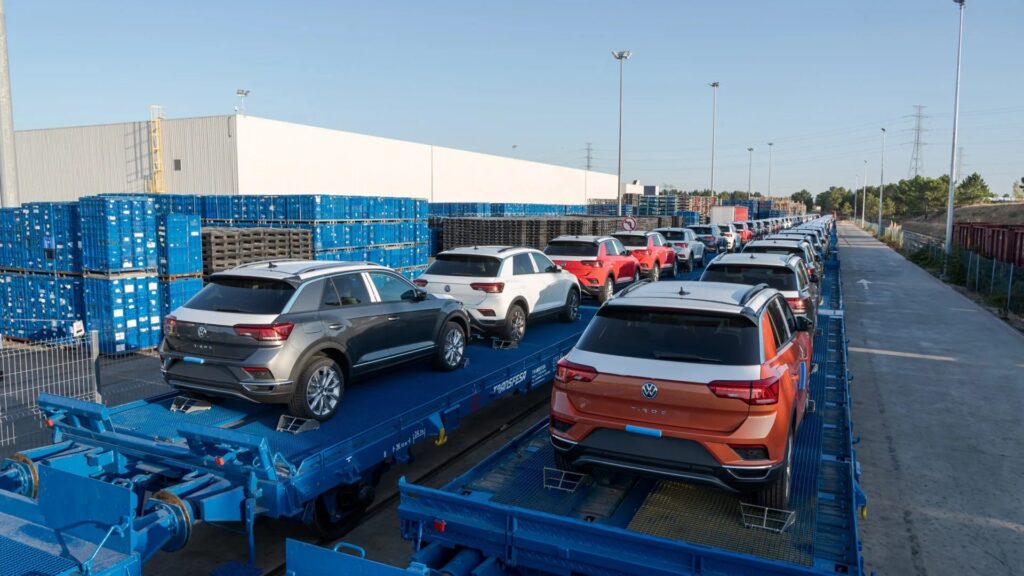
Esta capacidade produtiva permite-lhe ter um peso importantíssimo na balança comercial, assegurando 4,7% das exportações nacionais em 2020 e 6% em 2019 bem como 1,8% e 1,4% do PIB em 2020 e 2019, respetivamente.
2. Toyota Caetano – Ovar
A unidade fabril da Toyota, localizada em Ovar, tem uma importância histórica enorme. Foi a primeira fábrica do construtor japonês na Europa, inaugurada no ano de 1971. Faz, portanto, 50 anos de produção automóvel nacional!
Chegada ao mercado português pelas mãos da Salvador Caetano, a Toyota era nos anos 70 um fabricante à procura de disputar o mercado europeu e mundial. Afinal, o que acabou por fazer com extraordinário sucesso nas décadas seguintes, diga-se… Assim, esta foi a sua “porta de entrada” na europa, numa altura onde existiam elevadas barreiras à importação.
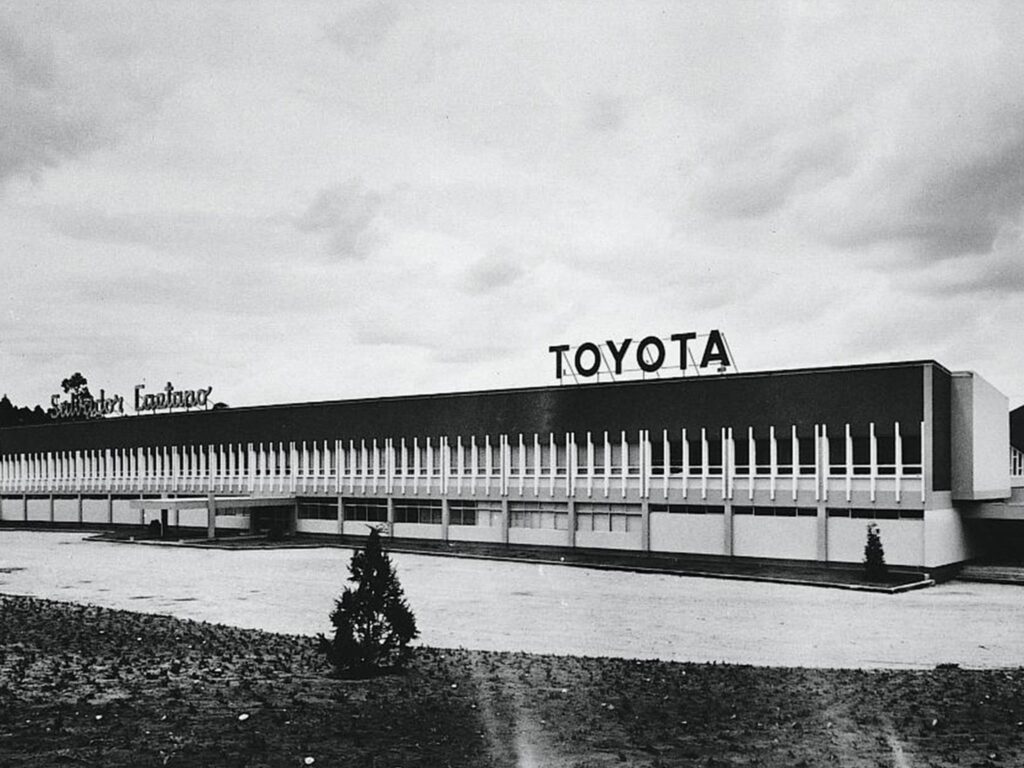
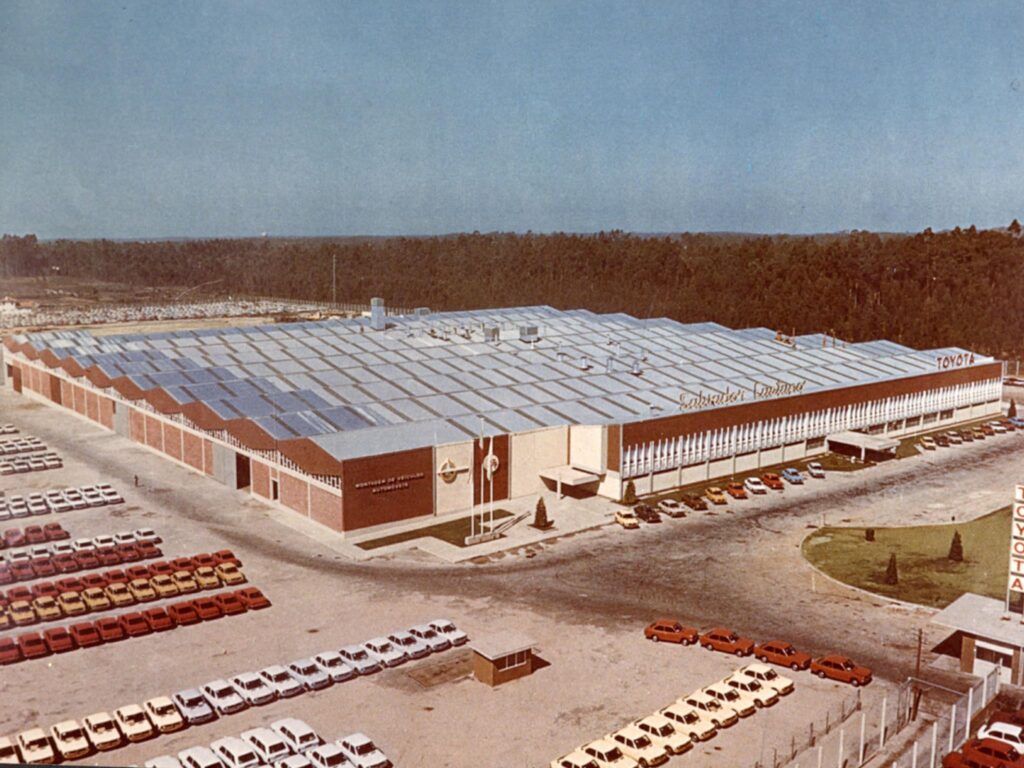
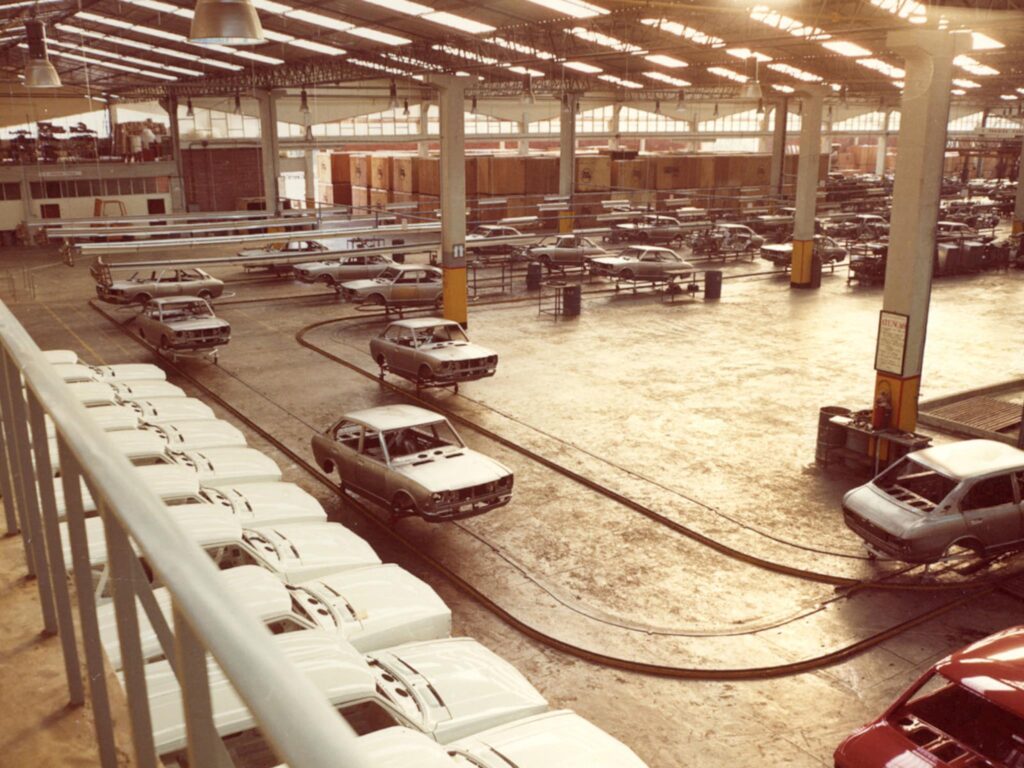
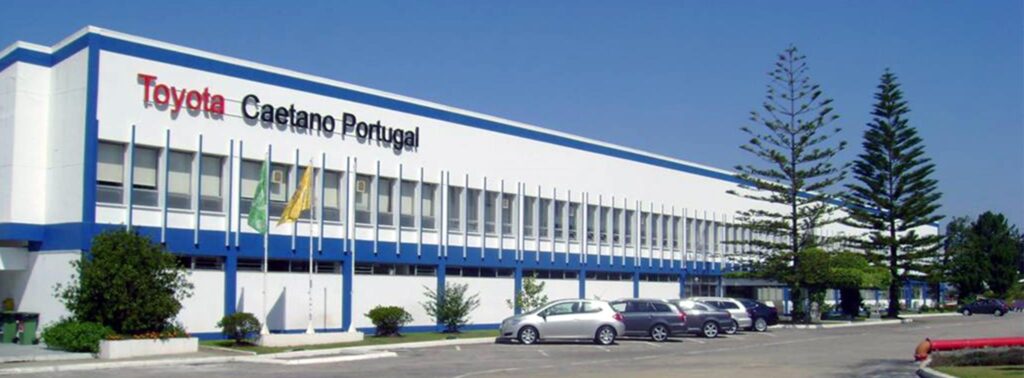
A produção iniciou-se com o Corolla seguindo-se o Corona e o Starlet. No entanto produziram-se três modelos de grande sucesso que ainda encontramos regularmente nas nossas estradas. A Dyna, a Hiace (a partir de 1979) e a Hilux (a partir de 1981).
Com um historial de produção no qual a sua mão de obra foi capaz de superar os exigentes índices de qualidade que a Toyota aponta para as suas fábricas, e em virtude da sua importância histórica, a marca decidiu manter a fábrica aquando do final de produção da Dyna.
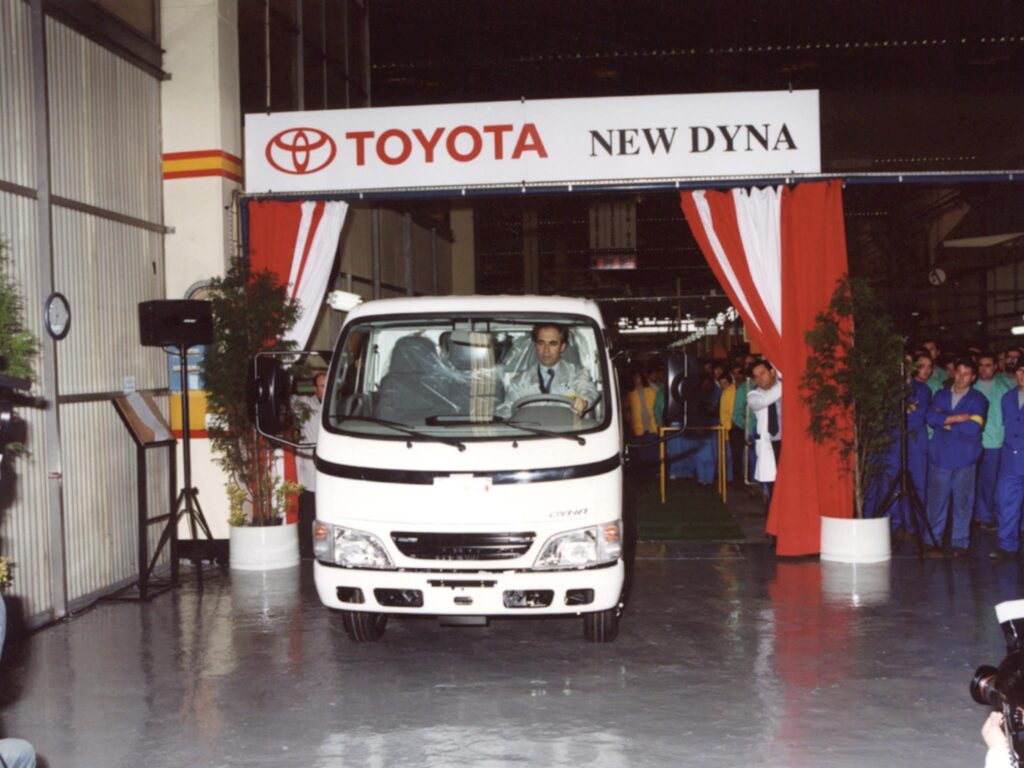
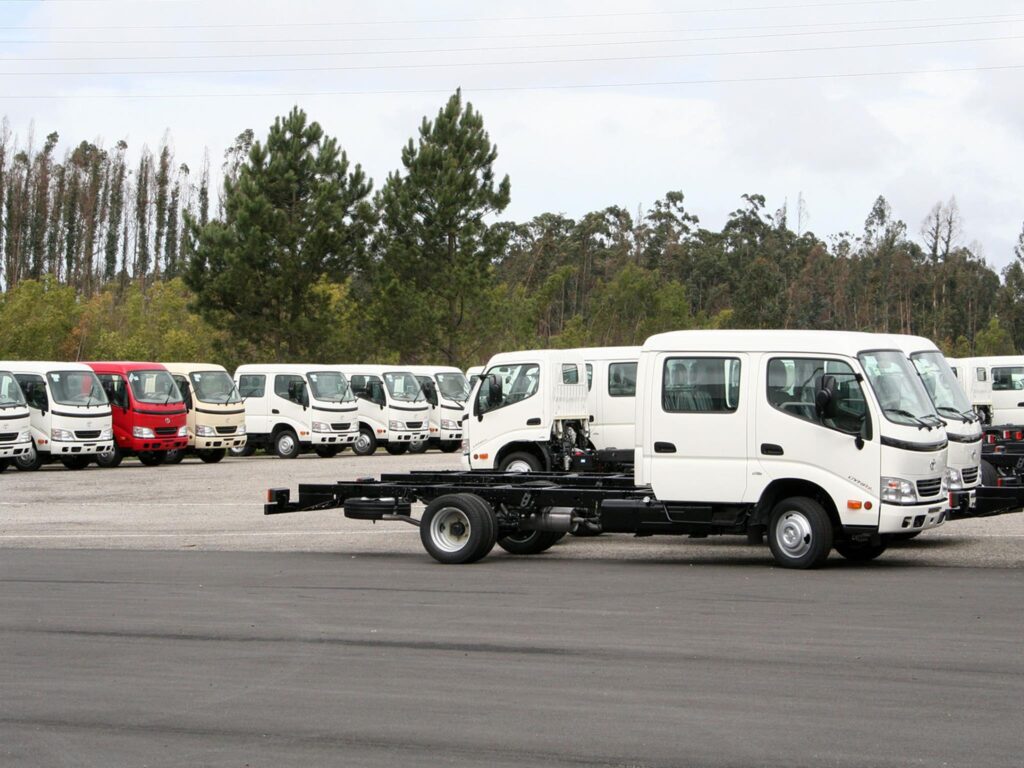
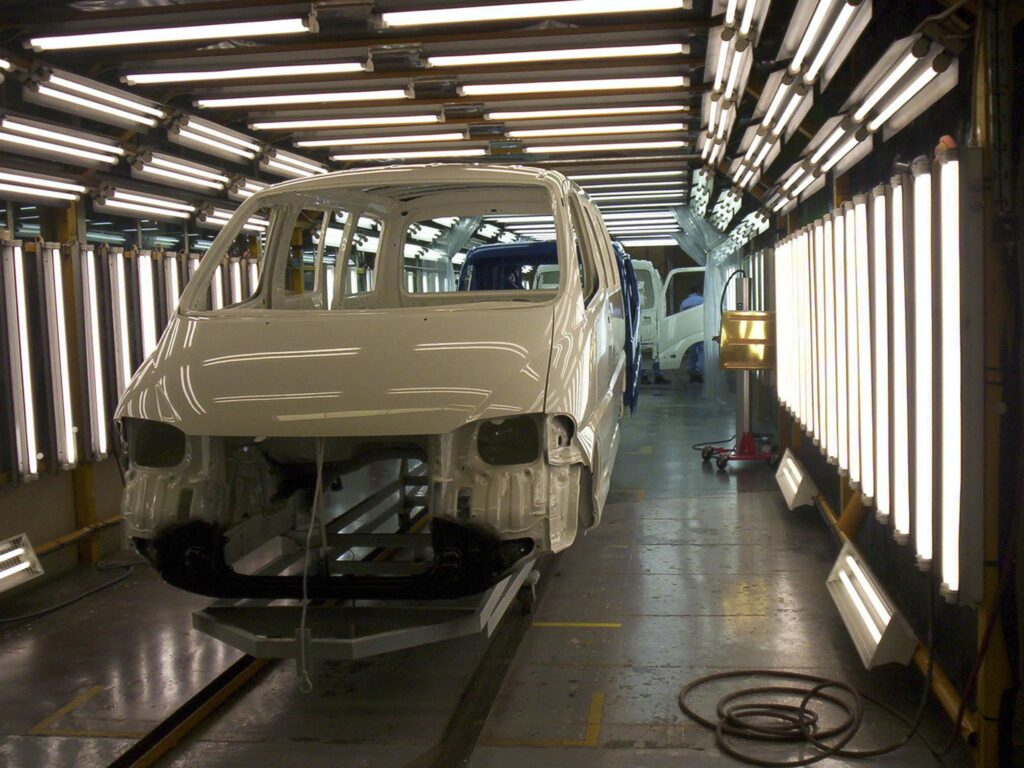
Assim, em julho de 2015, Ovar recebeu a fabricação do todo o terreno Land Cruiser 70, na primeira vez que este foi produzido fora do Japão. Desse modo, atualmente a totalidade da produção tem como destino a África do Sul.
O Land Cruiser 70 é o modelo atualmente em produção em Ovar
Neste momento a fábrica da Toyota Caetano em Ovar conta com 180 colaboradores e tem uma capacidade de produção que ascende ás 4500 unidades/ano nos seus 34 490 m2 de espaço com um único turno. Cada uma das unidades Land Cruiser 70 recebe aproximadamente 1000 componentes recebidos em CKD’s do Japão e desalfandegados no local. A fábrica de Ovar é a única que é simultaneamente um posto alfandegário.
Em Ovar montam-se os Land Cruiser 70, com as carroçarias e os chassis soldados essencialmente recorrendo a processos manuais. Mais recentemente a fábrica recebeu alguns robots, com a finalidade de aperfeiçoar o processo de soldadura. Para além disso, o objetivo passou por libertar meios humanos para outras tarefas e processos de igual importância. Sob o mesmo ponto de vista, e durante a visita que fizemos para este trabalho foi-nos garantido que nenhum posto de trabalho foi extinto. Afinal, as pessoas ainda contam!
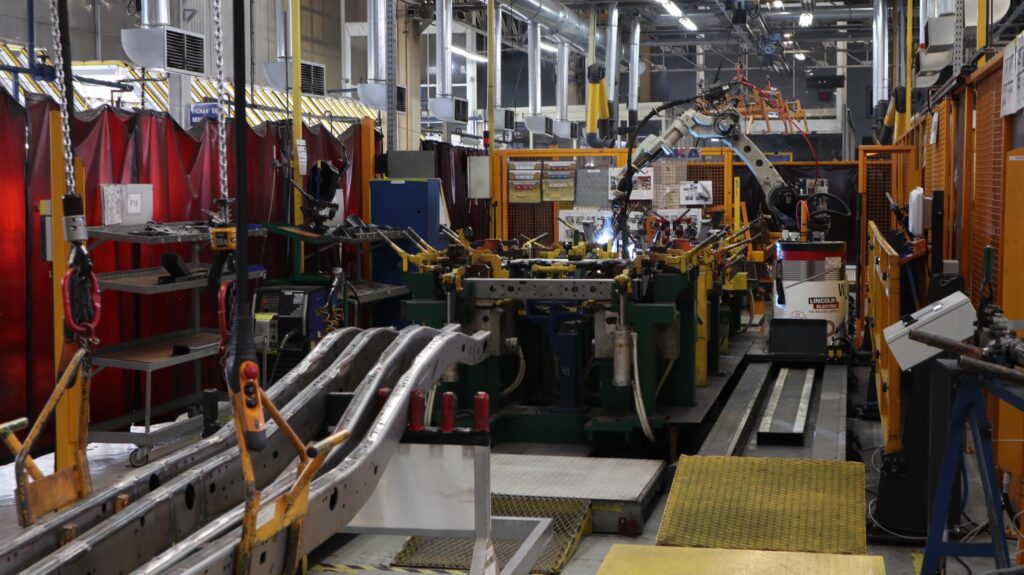
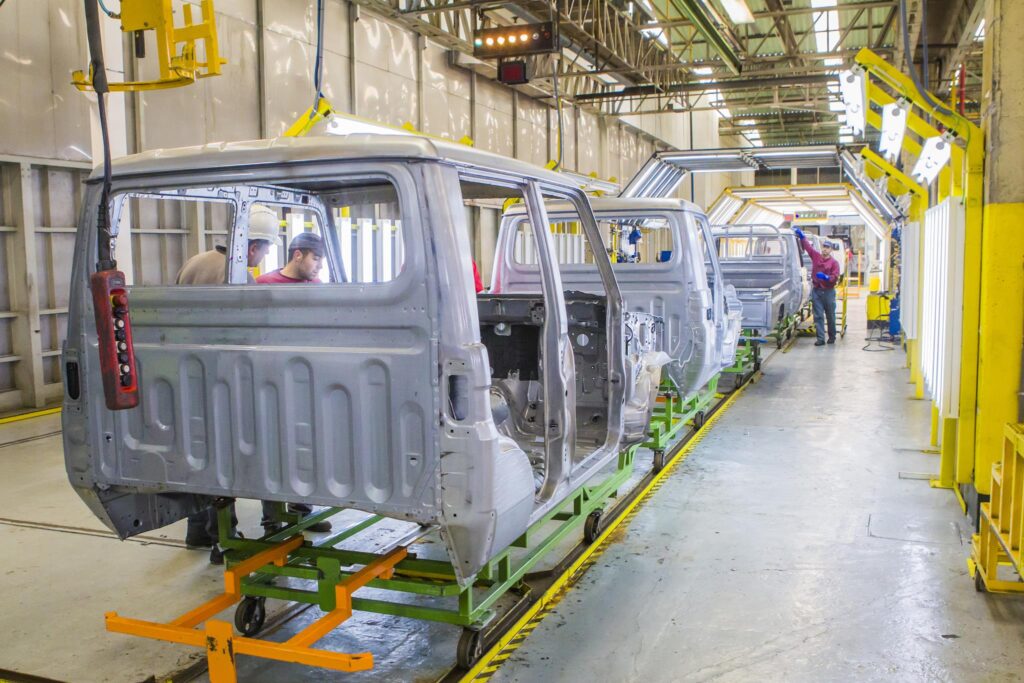
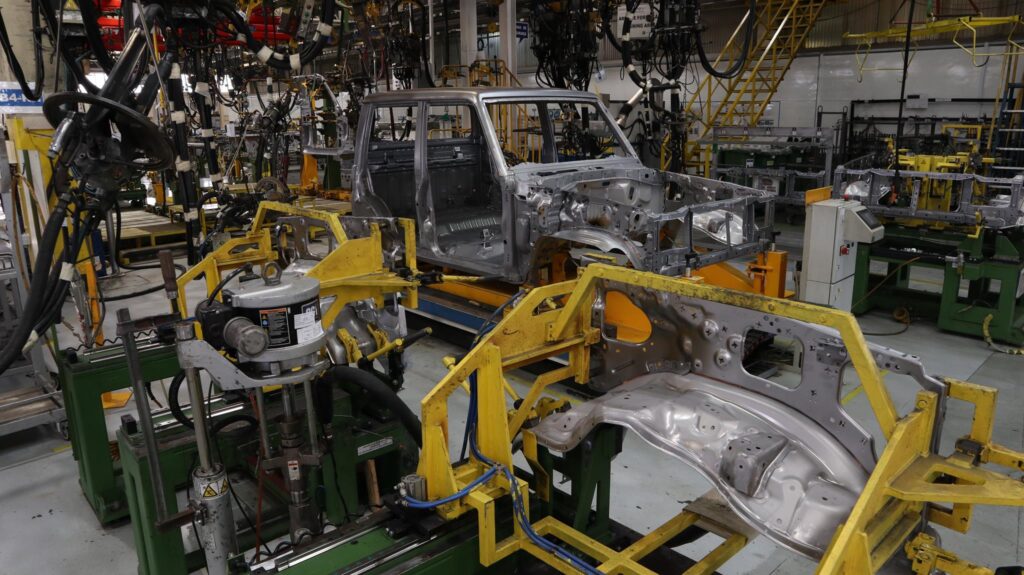
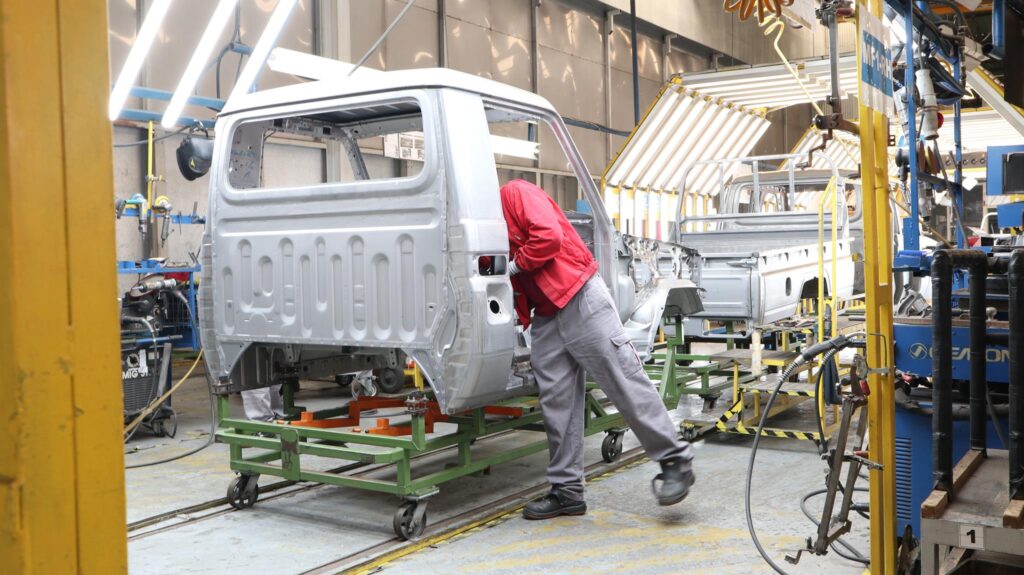
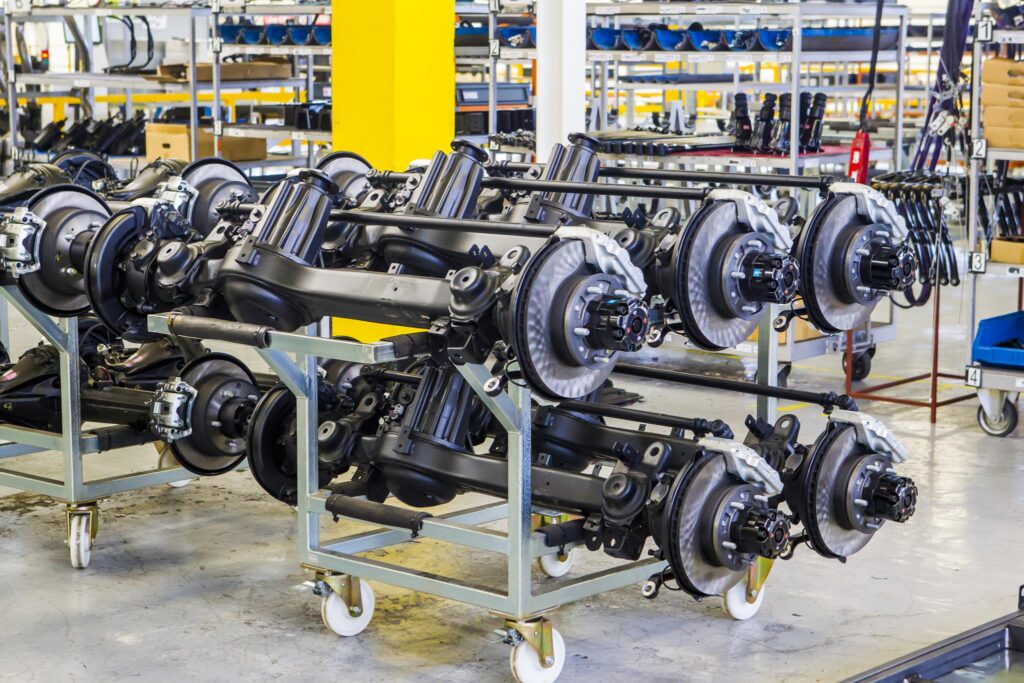
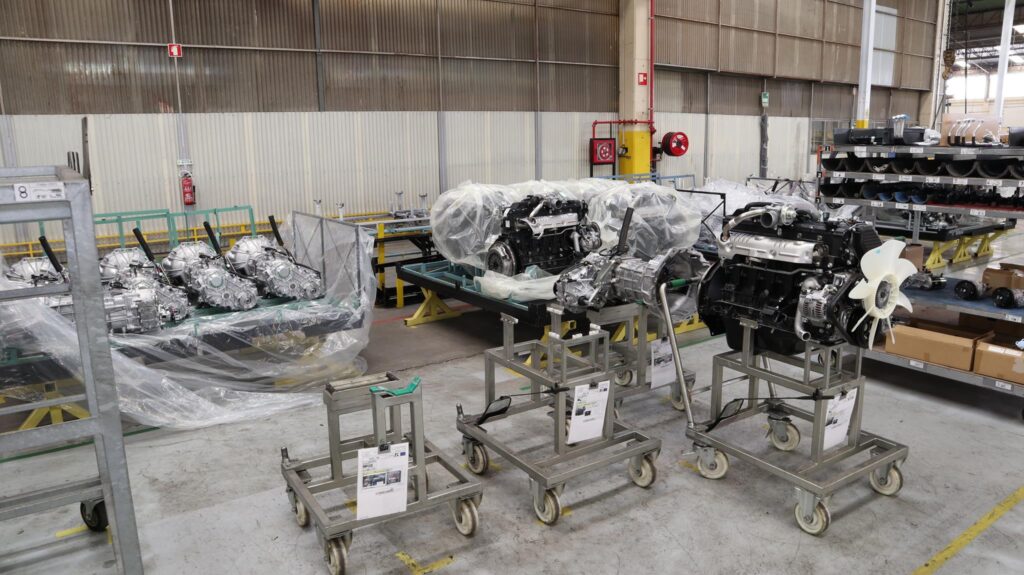
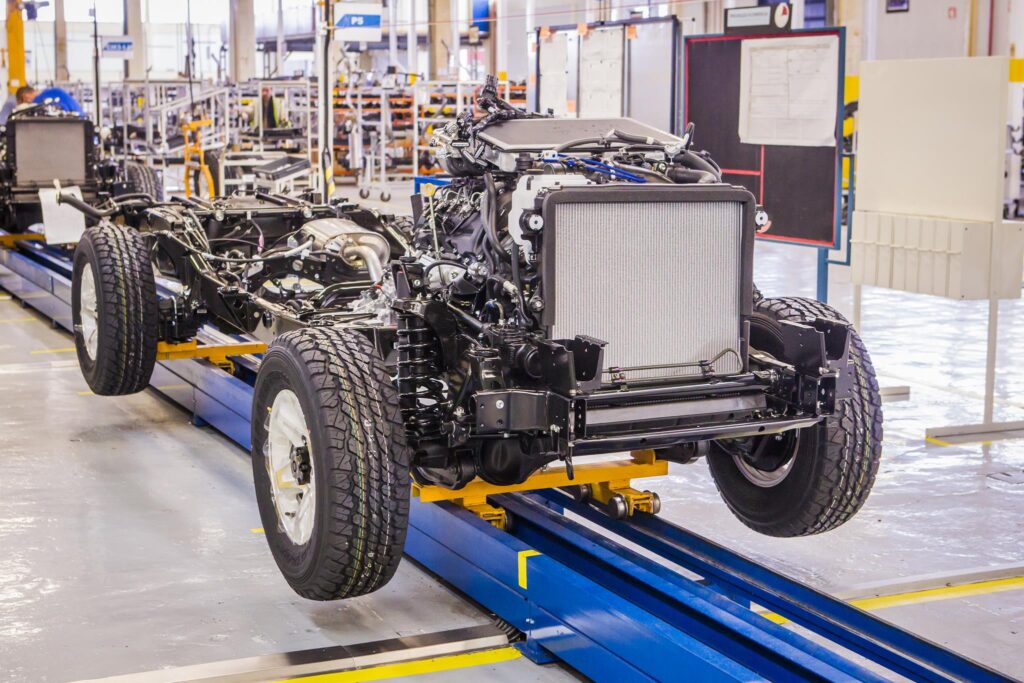
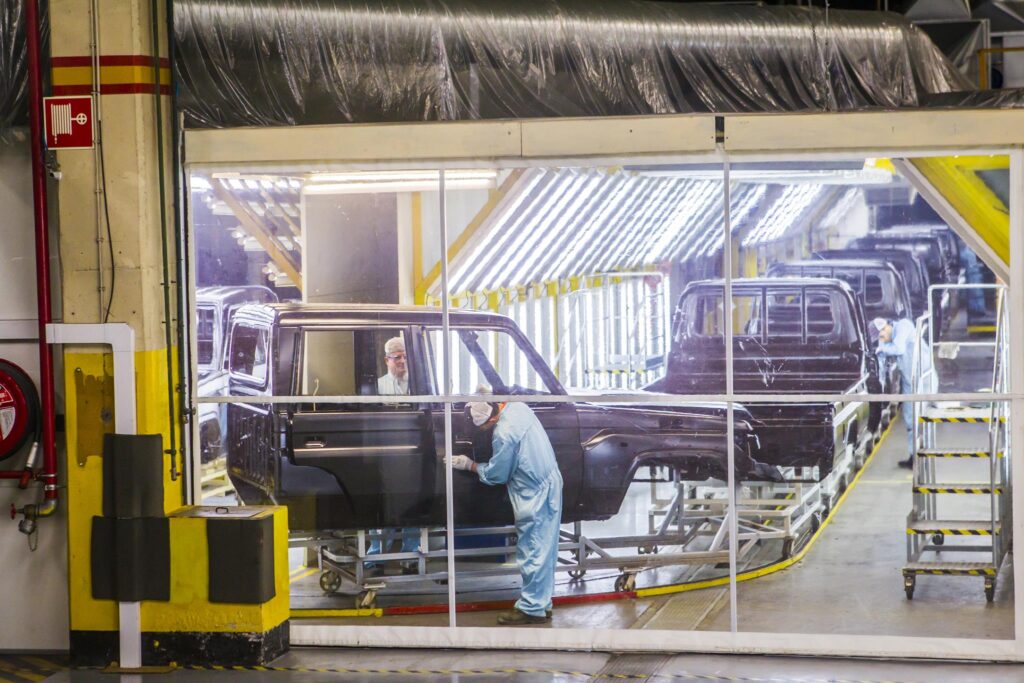
Por outro lado, alguns dos JIG’s usados na soldadura são construídos por empresas portuguesas. A pintura de duas camadas é feita manualmente à pistola e segue depois para a montagem. Nesta, a cabina une-se com o chassis e fazem-se os ajustes finais. O processo termina com dois rigorosos testes. Um primeiro ainda no final da linha de montagem, e outro já no exterior.
Todos os Land Cruiser são rigorosamente testados ainda na fábrica de Ovar
Os Toyota Land Cruiser 70 saem de Ovar para o porto espanhol de Santander, de onde são despachados para Durban, na Africa do Sul. A partir de 2018 as “caixas” vazias dos CKD’s são posteriormente devolvidas ao Japão parcialmente desmontadas.
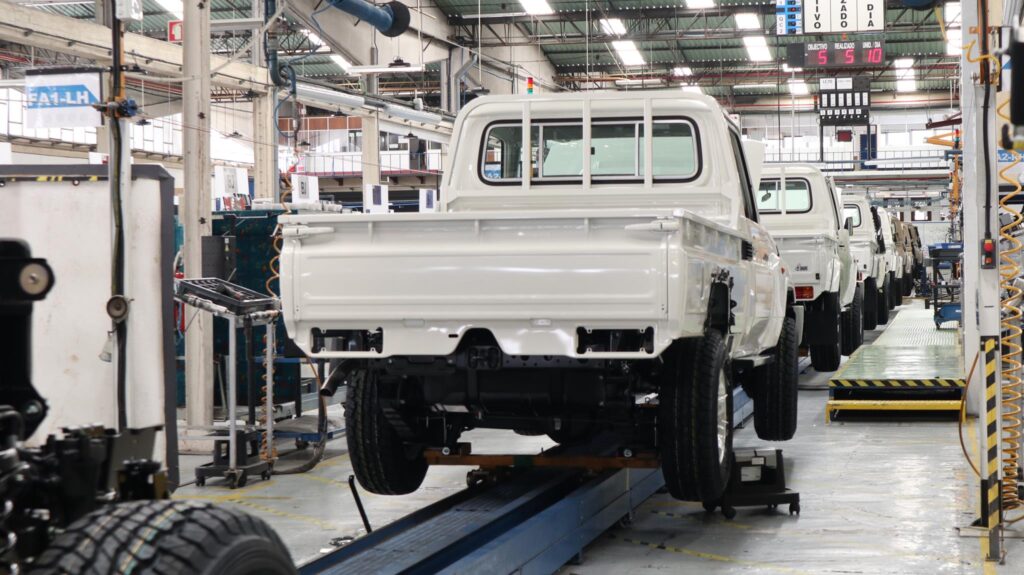
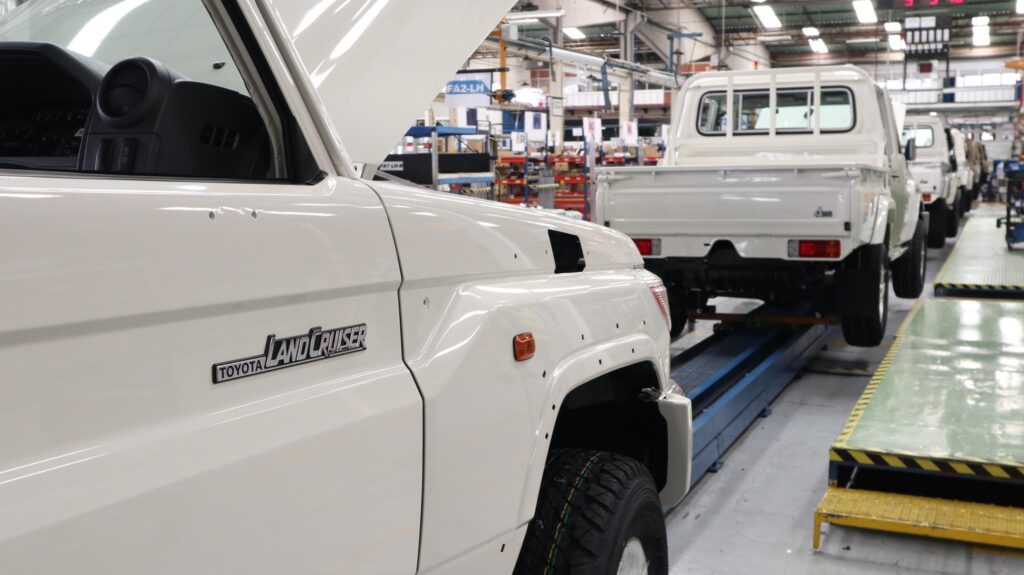
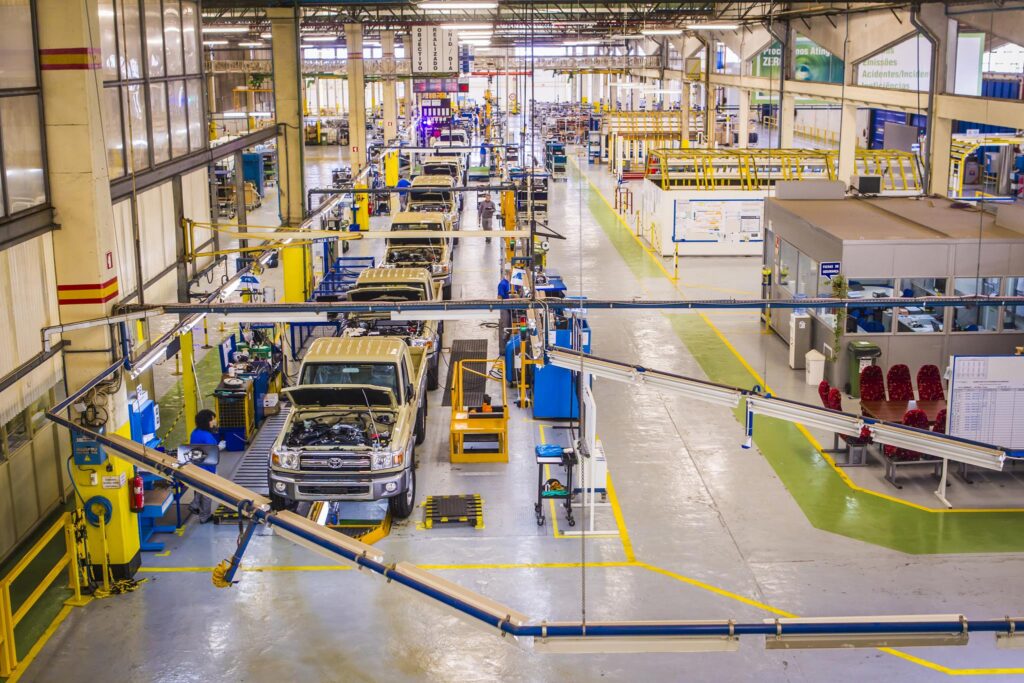
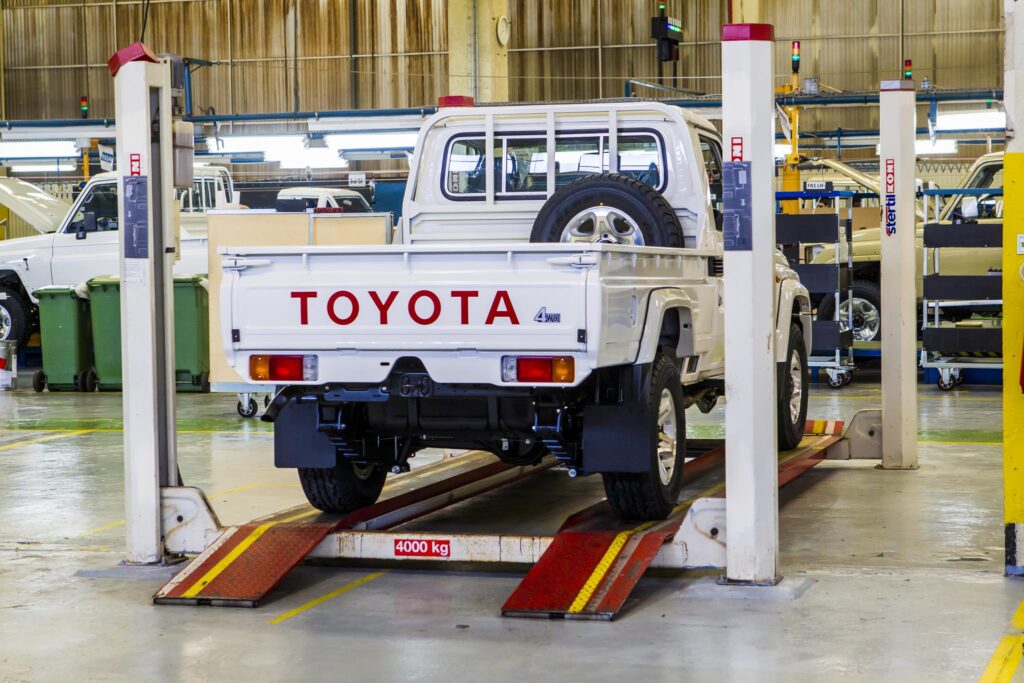
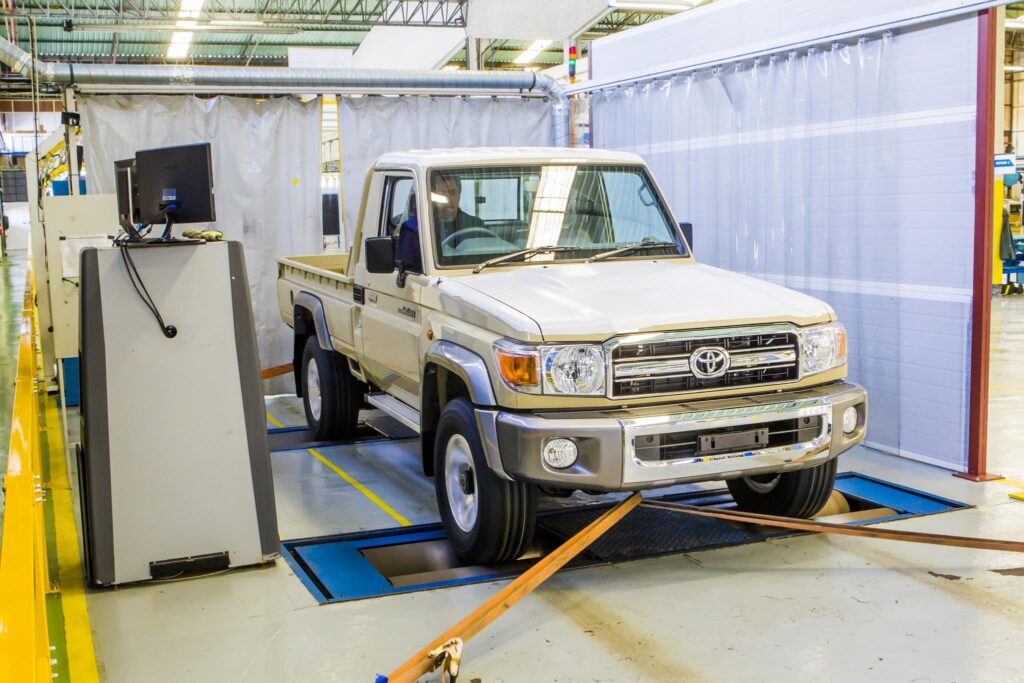
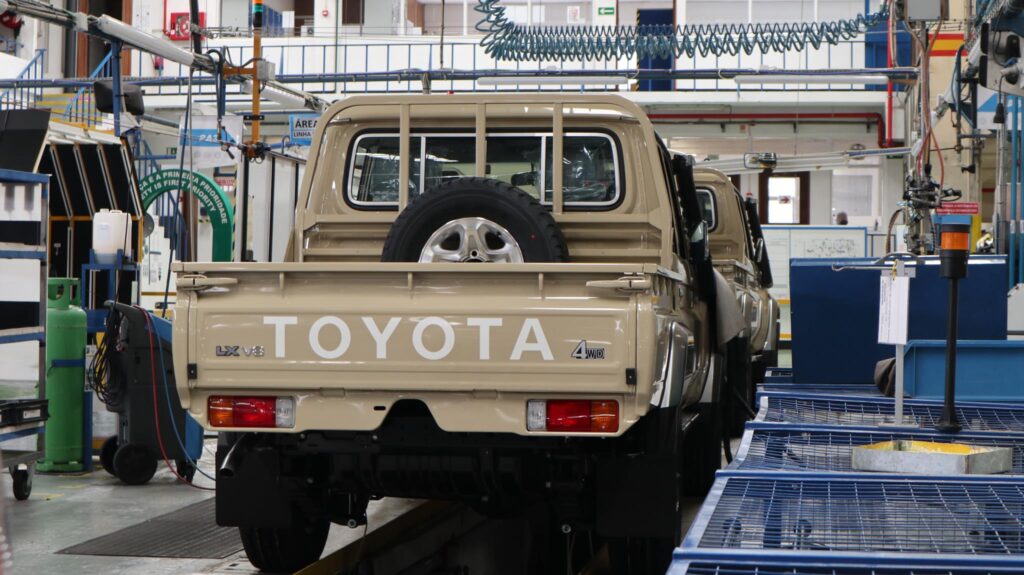
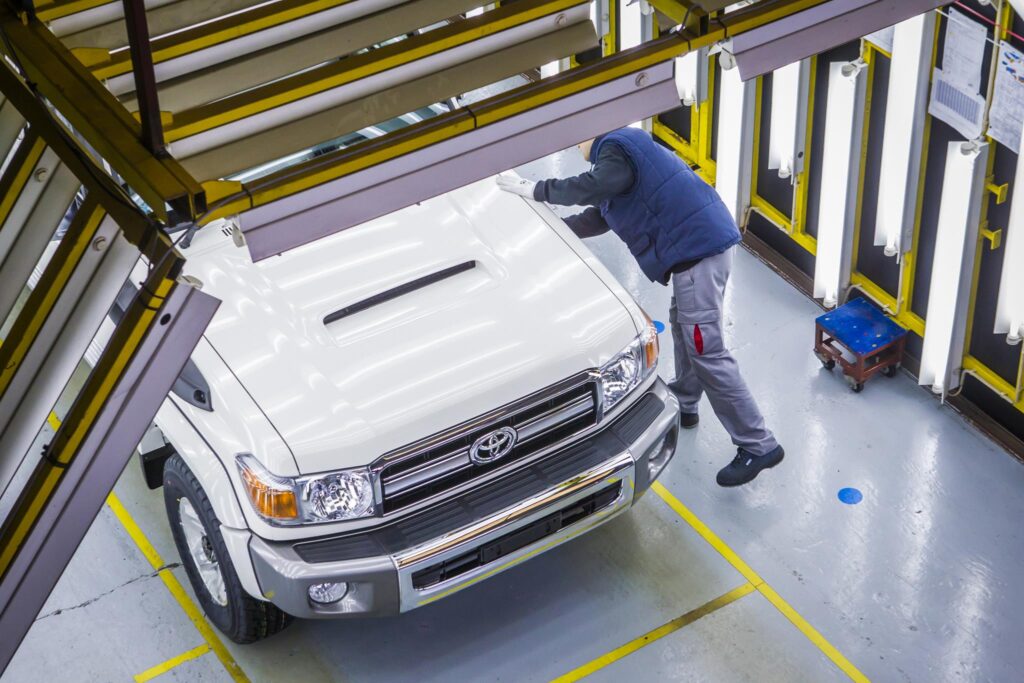
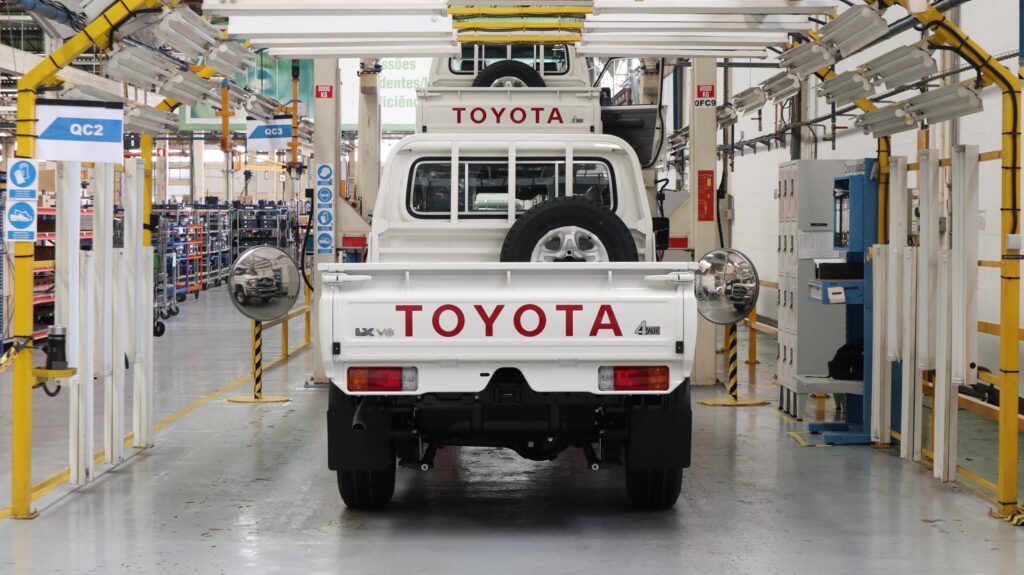
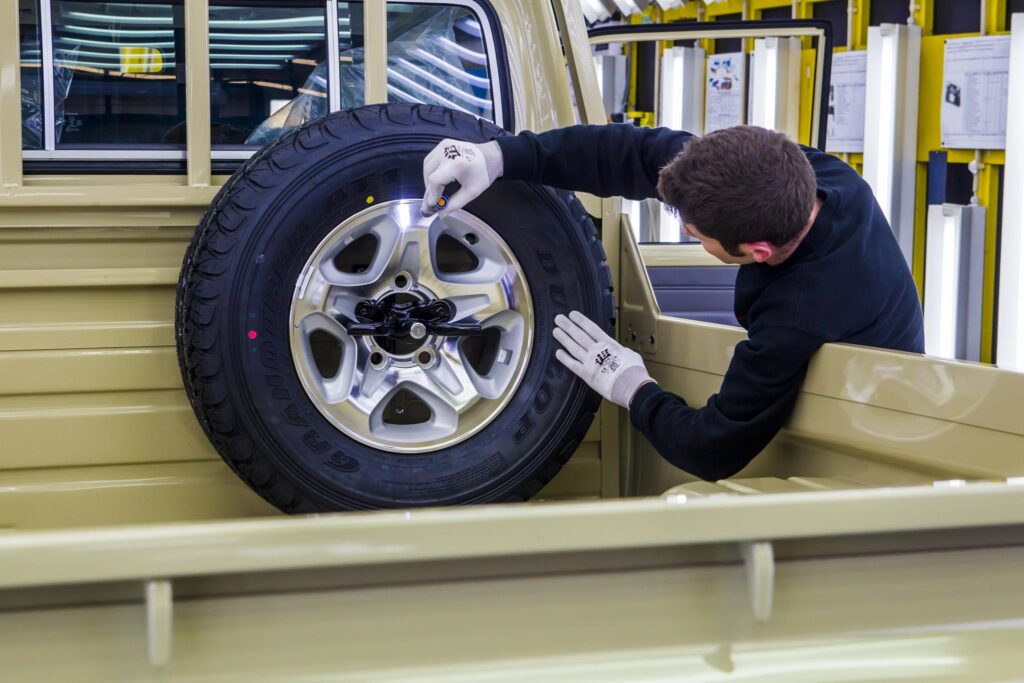
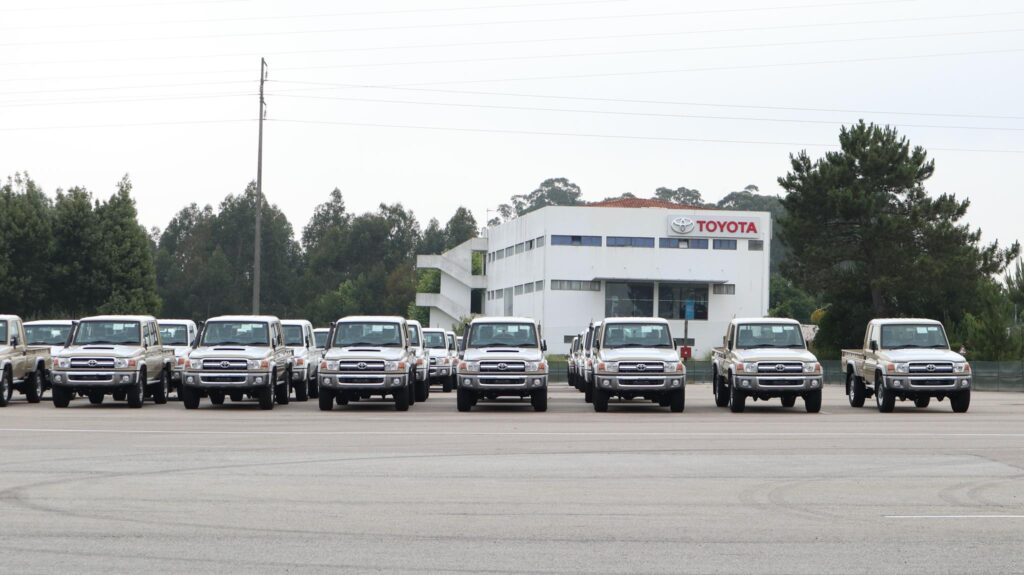
Desde a sua abertura, mais de 309 000 unidades saíram da linha de montagem de Ovar, sendo que em 2019 a produção foi de 2393 unidades, valor que desceu para as 1465 unidades em 2020, devido à pandemia.
Adicionalmente também os autocarros a hidrogénio com pilha de combustível proveniente da Toyota são montados em Ovar.
3. Grupo PSA – Mangualde
Fundada em 1962, a fábrica da Citroën localizada em Mangualde começou por produzir o emblemático 2CV sob patente. Desde que foi adquirida pelo construtor francês, em 1964, a fábrica foi responsável por um naipe de modelos carismáticos da Citroën. Assim, e além do 2CV, saíram da linha de Mangualde o AMI, o DS, a Dyane, o Mehari, o GS e o CX. Com efeito, o último 2CV produzido no mundo saiu de Mangualde em 1990. Posteriormente a fábrica produziu os bem sucedidos Citroën AX e Saxo.
Desde 1998 até ao momento, a fábrica produz os comerciais ligeiros do grupo PSA, respetivamente, Citroën Berlingo, Peugeot Partner/Rifter e Opel Combo. Atualmente integrada no grupo Stellantis, a unidade de produção de Mangualde produziu mais de 1,4 Milhões de veículos. A produção diária ascende aos 333 veículos e é assegurada por 900 colaboradores, a trabalhar em três turnos.
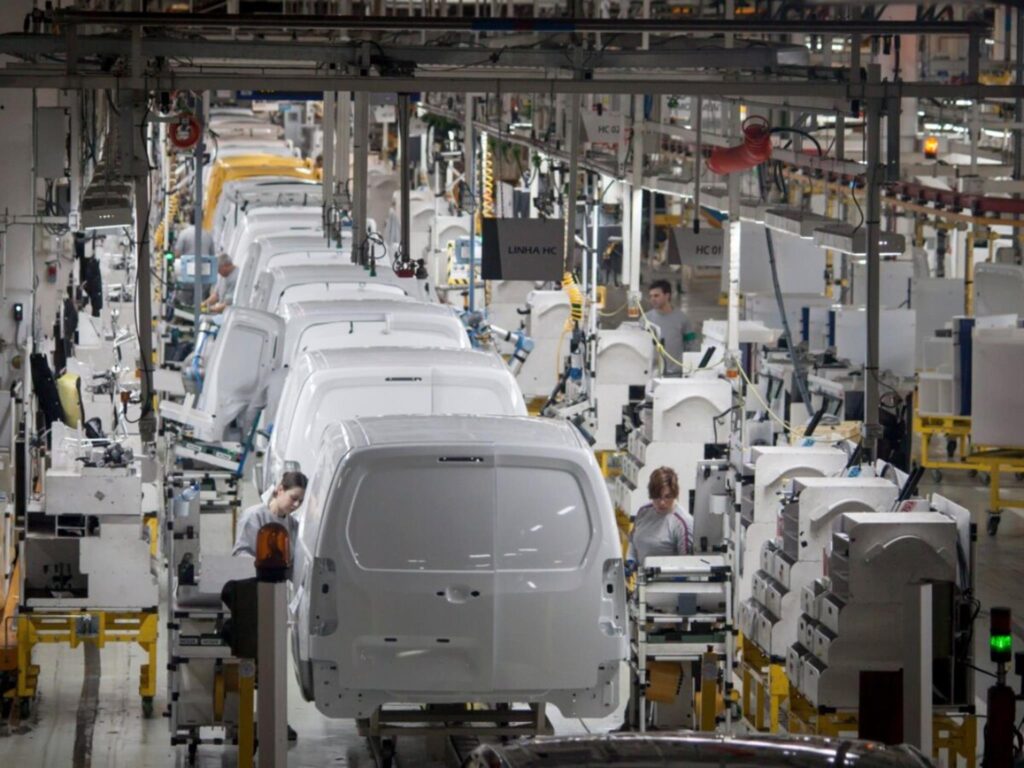
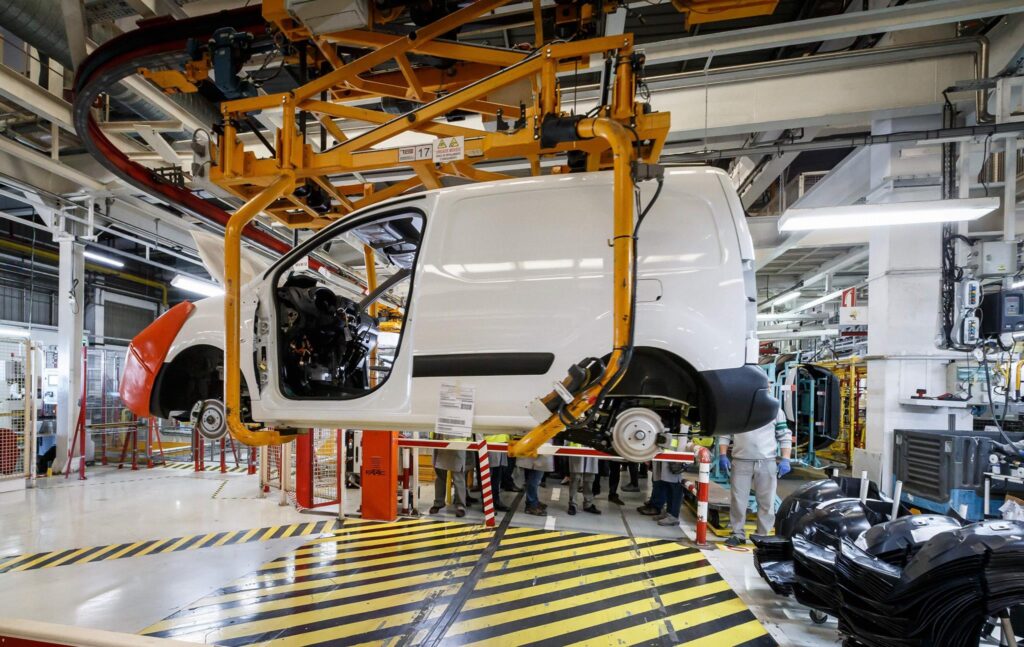
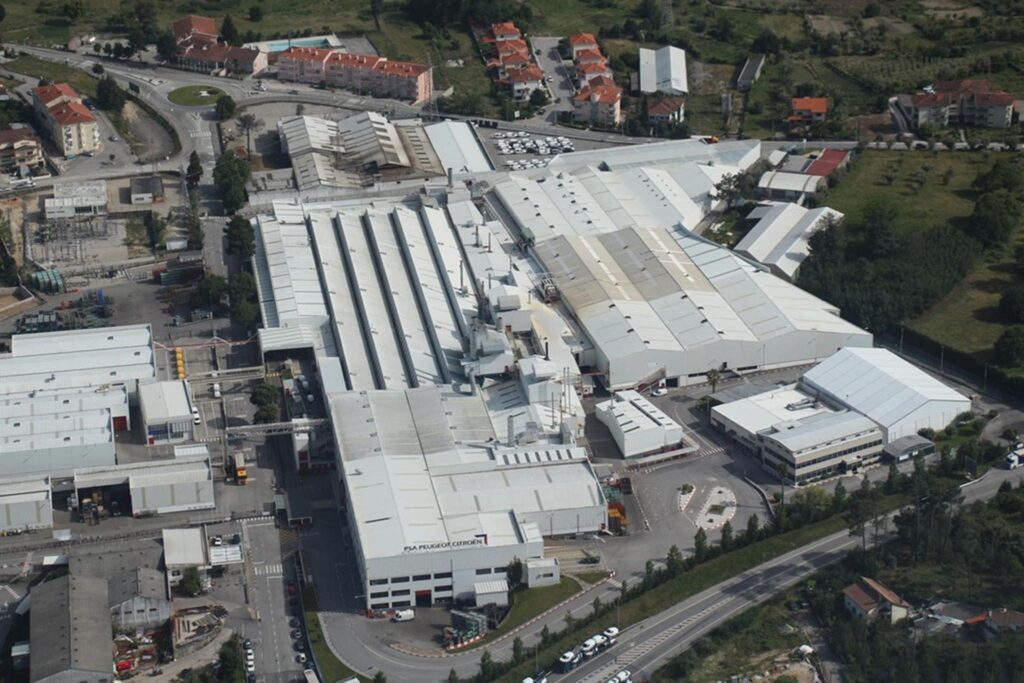
Em 2020 a equipa da PSA Mangualde produziu um total de 64 659 unidades, ao passo que em 2019, antes da pandemia, 77 606 unidades saíram da linha de montagem inserida nos seus 78 257 m2.
Em Mangualde a fábrica PSA produz modelos para a Citroën, Peugeot e Opel
Com uma ligação muito estreita com a fábrica espanhola de Vigo, Mangualde recebe desta as peças metálicas (em CKD) que compõem as carroçarias. Contudo, a soldadura e construção das mesmas já se faz em território nacional. Após o tratamento anti corrosão as carroçarias são pintadas e assembladas. Analogamente chegam de Vigo muitos dos 2050 componentes montados em cada unidade e muitos dos 600 parafusos a apertar. Da mesma forma é também na montagem que os comerciais recebem motor, suspensão e interiores.
Posteriormente a produção termina com o habitual teste de qualidade e verificação de alinhamentos, folgas e estanquicidade.
4. Mitsubishi Fuso Trucks – Tramagal
Situada no Tramagal, Abrantes, a fábrica atualmente propriedade da Fuso Trucks é a mais antiga em laboração no nosso país. Construída em 1964 pela Metalúrgica Duarte Ferreira começou por produzir camiões Berliet destinadas ao exército. Só em 1980 a fábrica passou a montar veículos da Mitsubishi, nomeadamente as L200, L300 e o Pajero. Todavia em 1990 deu-se a aquisição pela casa-mãe da Mitsubishi e desde 1996 que produz a Canter nos seus 39 900 m2.
Desse modo, conta com 440 colaboradores diretos e é o maior empregador do Município de Abrantes e um dos principais da região. Tendo produzido mais de 200 000 unidades desde a sua fundação, a única fábrica da FUSO Trucks na Europa está em vias de atingir a neutralidade carbónica, o que se estima para 2022. Esse processo implica instalar painéis solares para produção de energia, bem como utilizar a eCanter, o modelo 100% elétrico do modelo, na frota interna da fábrica.
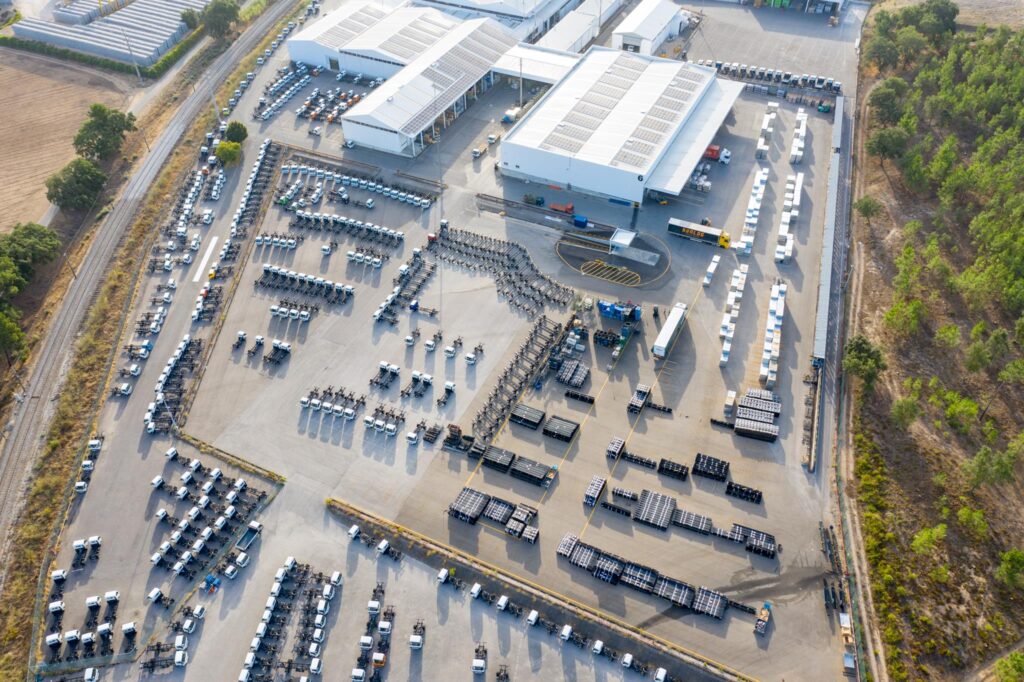
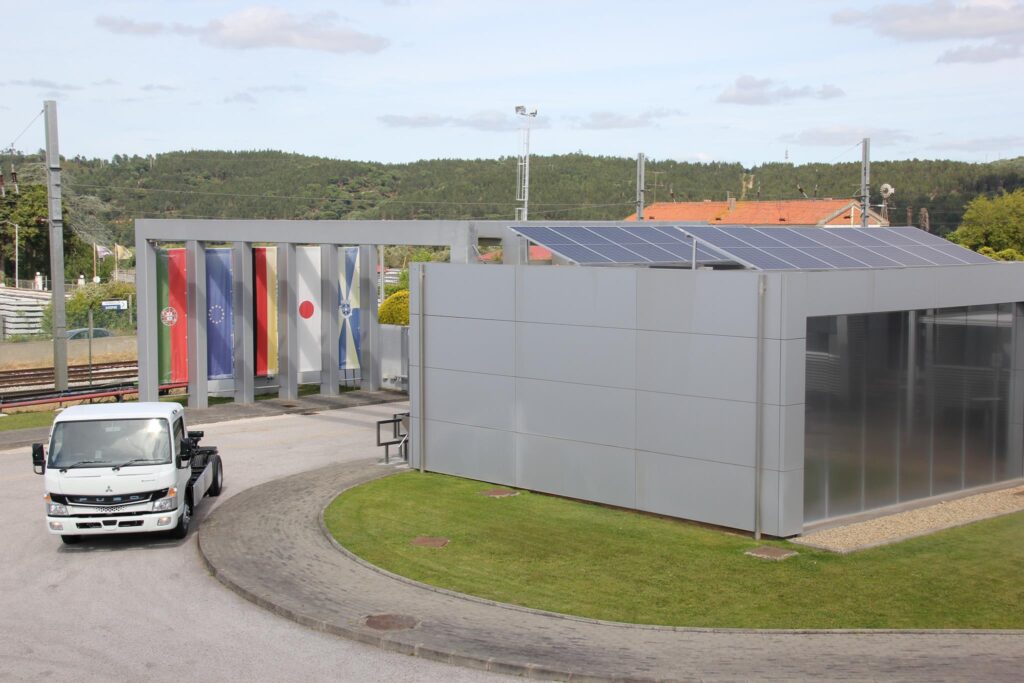
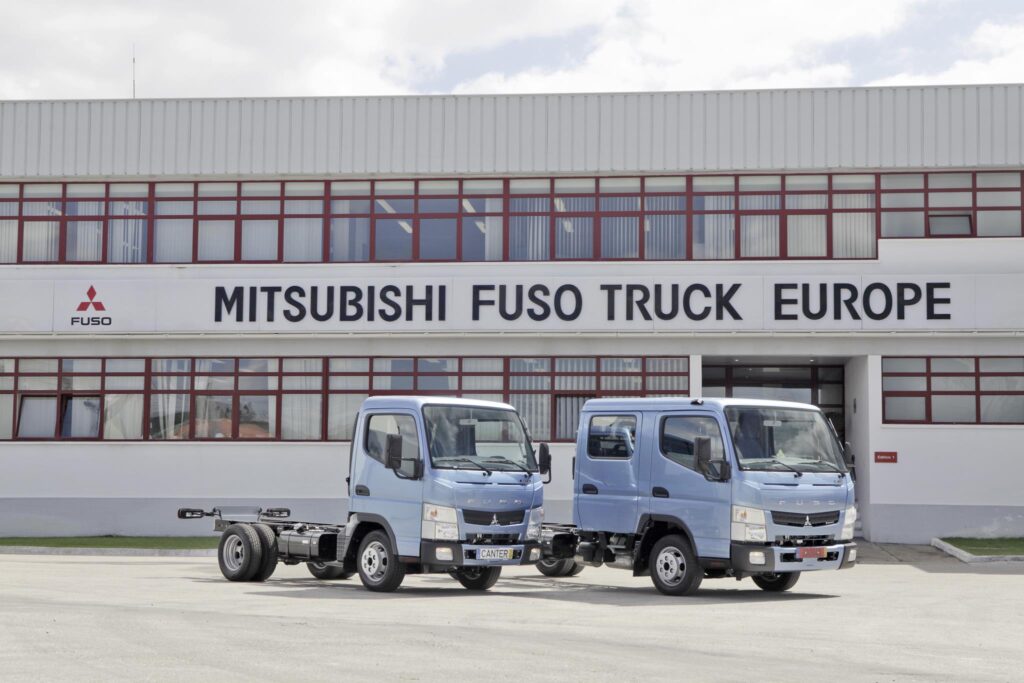
Denominada Fuso Trucks e detida pelo grupo Daimler, a unidade de produção do Tramagal assegura em exclusivo a montagem da Canter para todo o mercado Europeu e para mais alguns mercados, tais como Israel ou Marrocos, num total de mais de 30 países. Além disso, a eCanter, versão 100% elétrica, é também produzida nesta fábrica para todo o mundo naquele que é um produto fundamental para o futuro da unidade, bem como para a transição energética.
No Tramagal produzem-se unidades com motores a combustão Diesel, mas também as eCanter 100% elétricas
Com uma construção chassis/cabina, metade dos aproximadamente 3800 componentes que compõem a Canter vêm de 90 fornecedores europeus, ao passo que o remanescente provém do Japão, nomeadamente o chassis e a cabina. Também a caixa automática de dupla embraiagem tem origem Japonesa. Além do Japão, a maior parte dos componentes têm como origem Itália, Espanha e Portugal. As Fuso Canter recebem a pintura em Portugal, e não é uma surpresa dizer que a esmagadora maioria das unidades são de cor branca.
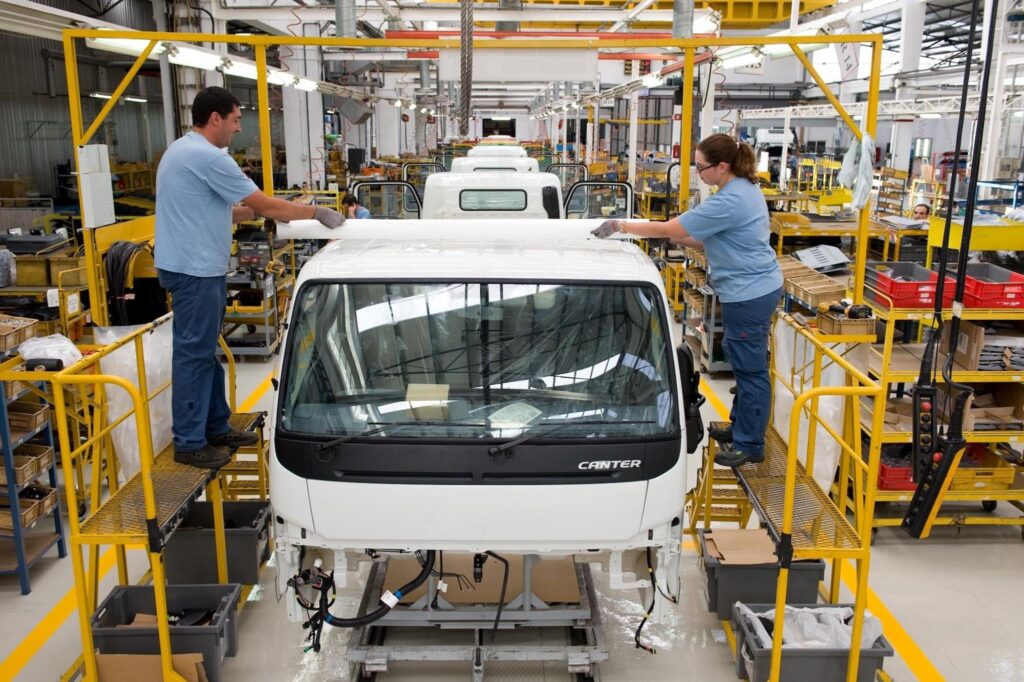
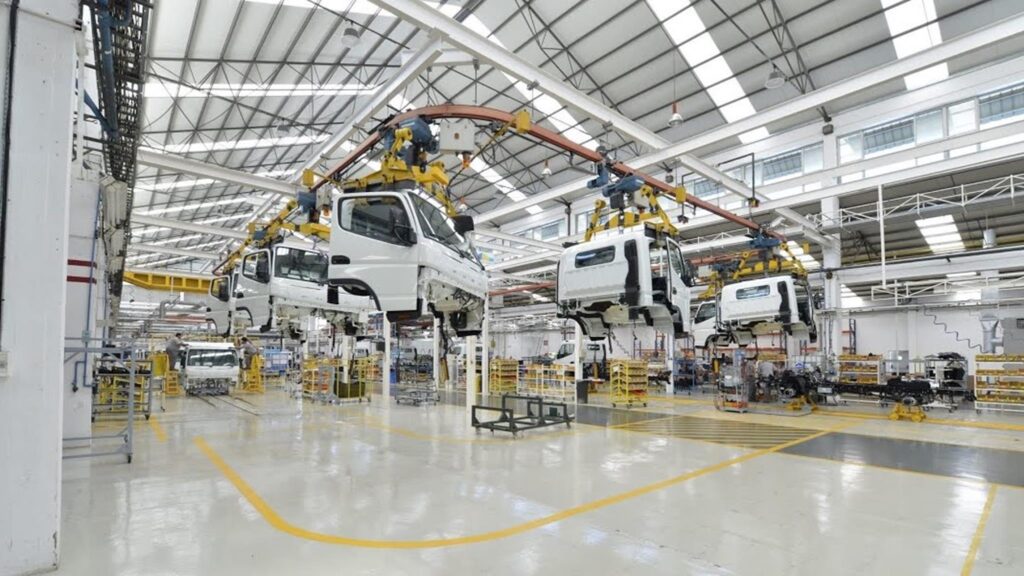
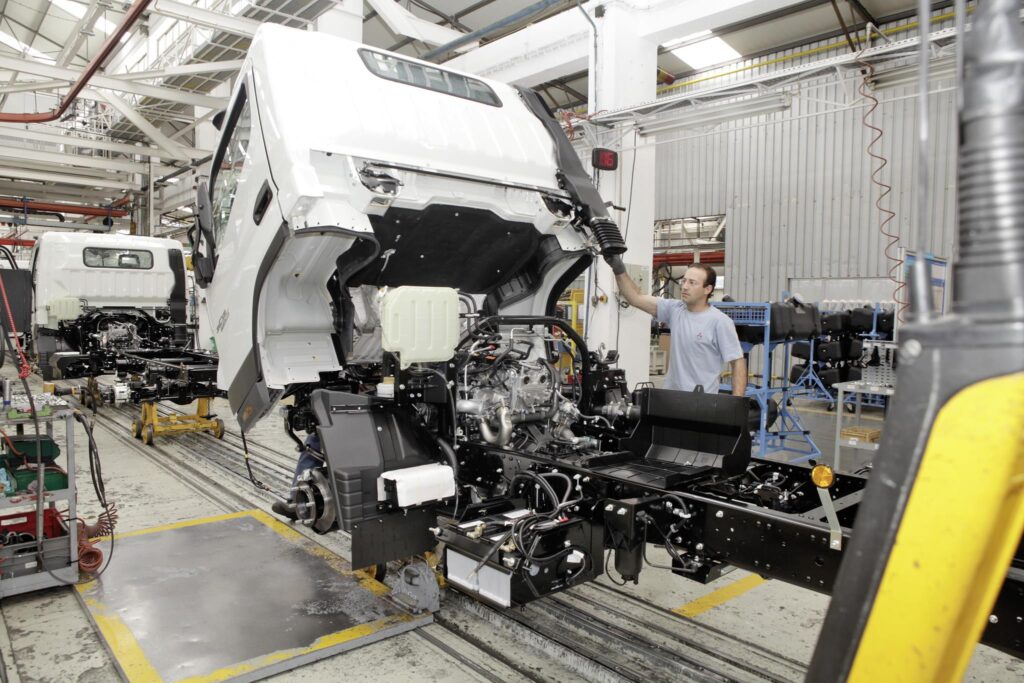
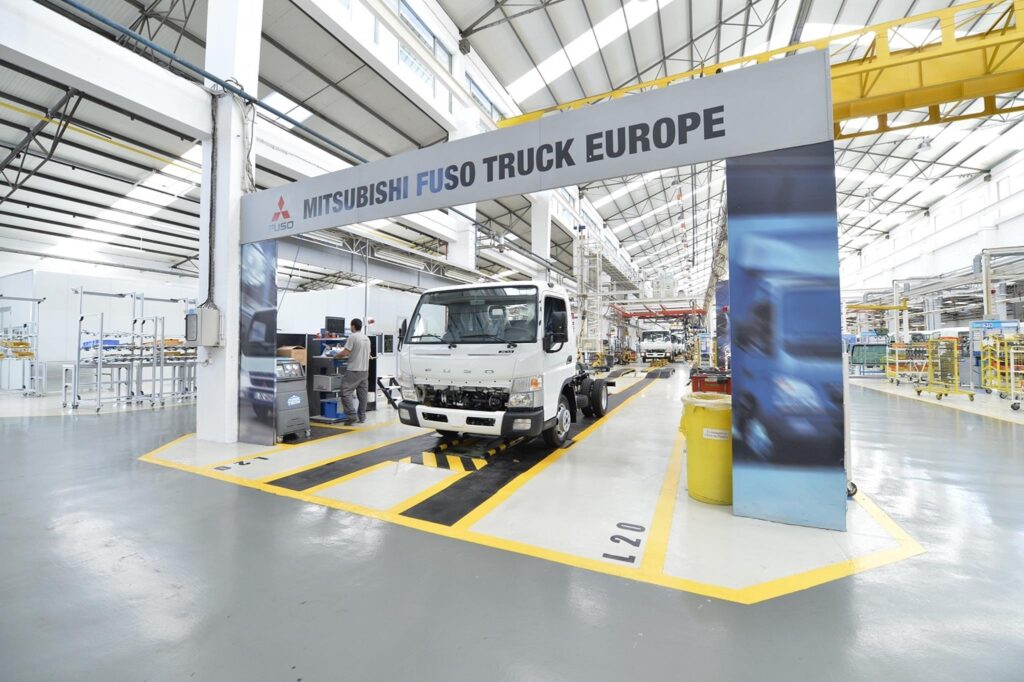
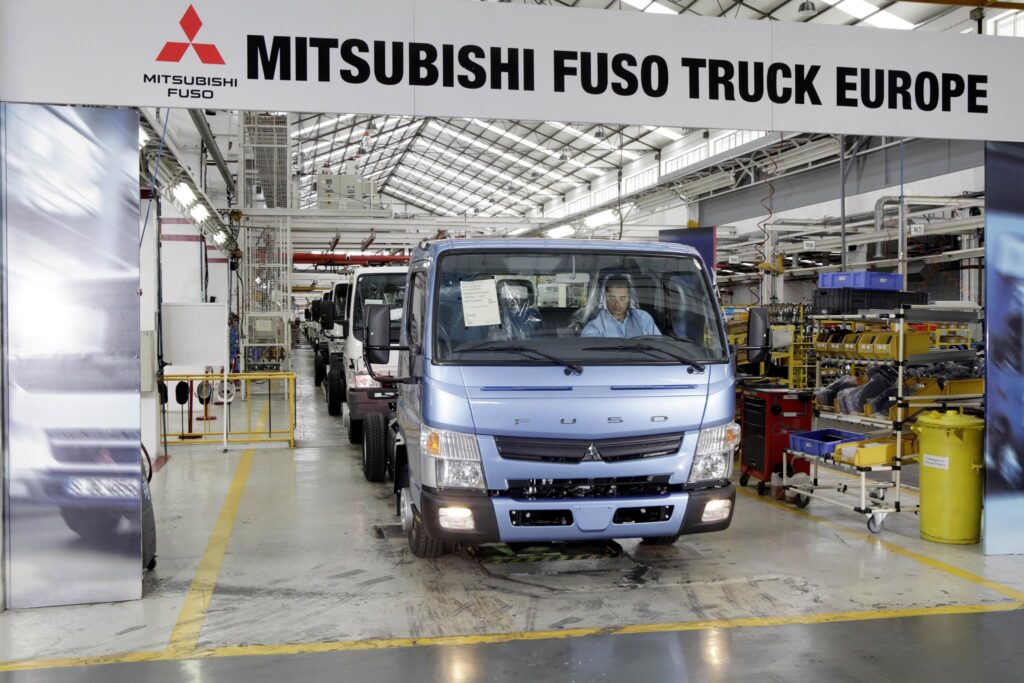
Logo após a pintura estar concluída, a cabina recebe vidros, janelas, cablagens e a totalidade do interior. Assim sendo está pronta para ser aparafusada ao chassis, que pode ter vários tamanhos e capacidades de carga. Após o controlo de qualidade a Canter está pronta a rolar.
Capaz de produzir 15 000 unidades com um único turno, ao ritmo de 48 por dia, no ano de 2019 a Mitsubishi Fuso Trucks do Tramagal produziu 8795 unidades, entre ligeiros e pesados. Da produção automóvel nacional exportada 80% ficou na Europa, sendo que se destacam 2241 unidades sem motor enviadas para os EUA. Em 2020 a produção total caiu para as 6051 unidades pois a produção esteve suspensa durante um período devido à pandemia de Covid-19.
Conclusão
Nem sempre reconhecida face à sua relevância, a produção automóvel nacional é muito importante enquanto indústria exportadora, não só pelo impacto que tem na balança comercial e no PIB, mas também pela capacidade de criar emprego especializado e transferir conhecimento.
Atualmente só estas quatro unidades fabris produzem mais de 6500 postos de trabalho diretos. Afinal, em Portugal produzem-se mais unidades automóveis do que aquelas que se que importam! Esperamos que com este artigo possas ficar a conhecer melhor “como nasce um automóvel” e o que se faz por cá! Até porque como vimos, a mão de obra nacional é reconhecida além fronteiras, o que obrigatoriamente nos enche de orgulho!